1969
Preparation of formaldehyde
Abstract
This
invention relates to an improved process for the preparation of
formaldehyde by oxidising methanol by air in the presence of a silver
catalyst and is characterised in that the gases leaving the
installation after separation of the condensable products, viz. water,
methanol and formaldehyde, are at least partly reinjected in the cold
state into the gaseous mixture leaving the catalyst layer. The present
invention relates to the preparation of formaldehyde by the known
process of oxidising methanol by air in the presence of a silver
catalyst. In this known preparation, a gaseous mixture of methanol and
air is passed at a suitable temperature over a silver catalyst. The
reaction products leave the catalyst layer at a temperature between
approximately 500*C and 650*C. These gases also contain the methanol
which has not reacted, as well as the desired formaldehyde, water,
nitorgen, carbon monoxide, carbon dioxide and hydrogen. It was proved
nitrogen, long time ago that in such a gaseous mixture, the temperature
of which is between approximately 500*C and 600*C, a certain number of
chemical reactions are liable to develop which are considered as
parasitic with respect to the main formation reaction of the
formaldehyde and which it is generally desired to minimise or suppress.
To this end, various methods have been advocated which can be summed up
more particularly in the use of an indirect heat exchanger and in the
use of atomization of water or a diluted solution of formol. Naturally,
it was the aim of the various known methods to lower the temperature of
the gases leaving the catalyst layer as quickly as possible to a value
lower than 350*C - 450*C. These methods of treating hot gases have
various drawbacks and it is an object of the invention to avoid or
minimise these drawbacks as far as possible. According to the present
invention, a method of preparing formaldehyde by oxidising methanol by
air in the presence of a silver catalyst is characterised in that the
gases leaving the plant after separation from the condensable products
(water, methanol and formaldehyde) ARE AT LEAST partly reinjected in
the cold state into the gaseous mixture leaving the catalyst layer. The
reinjected gases contain, more particularly, nitrogen, carbon dioxide,
carbon monoxide and hydrogen. These gases are referred to as
''''tail'''' gases, and are cold, since they are obtained after
treating the gaseous mixture leaving the catalyst layer by known
methods having as an object, the condensation or absorption of the
condensable chemical products contained in this gaseous mixture. They
are, on the other hand, only of small value and are usually rejected to
atmosphere. However, used according to the invention, they allow the
yield from a plant for preparing the formaldehyde to be substantially
improved. This improvement in the yield is carried out following a
complex mechanism which has not yet been entirely elucidated. It is
caused certainly partly by the rapid cooling of the gaseous mixture
leaving the catalyst layer, in which the synthesis of the formal dehyde
is carried out: for this reason, it will be apparent that the
reinjection of the tail gases must be effected as near as possible to
the last layer of the catalyst bed and that it must be ensured, if
maximum improvement is to be obtained, that a good distribution of the
gases injected into the gaseous mixture leaving the catalyst is
effected. But it is also certain that the improvement of yield is
caused partly by the composition of the said tail gas. In order to
obtain maximum improvement of yield, it has been found, on the other
hand, that it was necessary to inject a quantity of tail gas into the
gaseous mixture leaving the catalyst layer, representing per molecule
of formol (formaldehyde) prepared approximately 1.7 times the quantity
of tail gases produced. This is why, according to the invention, such a
quantity of tail gas will be made to circulate and be reinjected into
the gaseous mixture and that the gaseous circuit will be cleared from
the excess gases produced as the reaction takes place. Amongst the
other advantages of the method according to the invention may be
mentioned: 1. The increase in the volume of inert gas resulting from
the recirculation enables the evaporation of a large part of the water
and methanol situated at the base of the first absorption tower, which
is a particularly interesting advantage when ureaformaldehyde
concentrates are to be produced by absorption by means of solutions of
urea. 2. This same increase of the gaseous volume leaving the reactor
facilitates thermal recuperation of the reaction heat by exchange,
whilst avoiding premature condensation in the exchangers, on account of
the partial decrease in pressure of the condensable part. 3. The
invention can be adapted immediately to methods using a circuit
operating at a pressure lower than atmospheric pressure throughout the
line with synthesis of transport for the gases situated at the tail of
the installation. Only the calibre of the compressor or ventilator used
is to be increased.
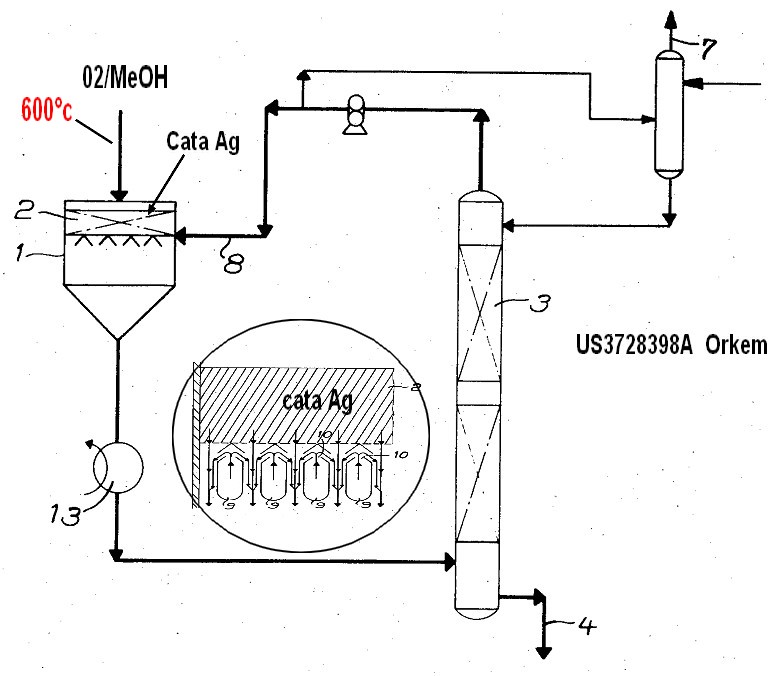
Publication number
Priority date
Publication date
Assignee
Title
DE1259323B
*
1964-10-02
1968-01-25
Chemische Maschb Werke Rudisle
Process for the production of aqueous formaldehyde solutions
* Cited by examiner, † Cited by third party
Publication number
Priority date
Publication date
Assignee
Title
US3965195A
*
1972-01-13
1976-06-22
Badische Anilin- & Soda-Fabrik Aktiengesellschaft
Process for the production of formaldehyde
US4072717A
*
1974-09-04
1978-02-07
Basf Aktiengesellschaft
Manufacture of formaldehyde
US4119673A
*
1974-09-18
1978-10-10
Basf Aktiengesellschaft
Manufacture of concentrated aqueous solutions of formaldehyde
US4390730A
*
1981-07-27
1983-06-28
Celanese Corporation
Formaldehyde production
* Cited by examiner, † Cited by third party, ‡ Family to family citation
Publication
Publication Date
Title
CA1143136A
1983-03-22
Process for producing methanol and ammonia
EP0326718B1
1991-12-11
A process for producing methanol
US4087513A
1978-05-02
Method of hydrolyzing urea contained in waste water streams
US6486218B2
2002-11-26
Method of manufacturing methanol
CA1112670A
1981-11-17
Process for manufacture of methanol
GB930213A
1963-07-03
Process for the preparation of urea
JP2857993B2
1999-02-17
Method for continuous production of aqueous formaldehyde solution
US3489515A
1970-01-13
Production of high percentage nitric oxide
JPH0662478B2
1994-08-17
Formaldehyde solution manufacturing method
US1858822A
1932-05-17
Process for the treating of hydrocarbon materials
US3137725A
1964-06-16
Heat recovery in urea synthesis process
JP4306320B2
2009-07-29
Process for producing dialkyl carbonate
***************************************************************
JPH0662478B2
1994-08-17
Formaldehyde solution manufacturing method
Formaldehyde solution manufacturing method
US
JP
KR
JPH0662478B2
久五 吉川
三菱瓦斯化学株式会社
Priority 1984-04-12 • Filed 1984-04-12 • Published 1994-08-17
[Claims] 1. A raw material gas containing methanol, air and water vapor
is catalytically reacted on a silver catalyst, and the resulting
reaction product gas is brought into contact with water to absorb
formaldehyde in the product gas into the water, thereby absorbing the
bottom of the absorption …
Claims (1) translated from Japanese
claims]
1.
A raw material gas containing methanol, air and water vapor is
catalytically reacted on a silver catalyst, and the resulting reaction
product gas is brought into contact with water to absorb formaldehyde in the product gas into the water, thereby absorbing the bottom of the absorption tower. To formaldehyde concentration 37 to 6
In the method for producing a 0% by weight formaldehyde solution, the amount of air per mol of the raw material methanol is 1.5 to
The total amount of water was 2.0 mol and the amount of water
corresponding to the amount of water vapor added to the raw material gas
and the amount of water necessary to dilute the product formaldehyde solution was added as absorption water from the top of the absorption tower,
In addition, the methanol concentration is 0.1 to 3.0 from the upper stage of the absorption tower.
Wt%, formaldehyde concentration of 0.1-1.0 wt% aqueous solution of the composition of 0.2 ~ per mol of the starting methanol
A method for producing an aqueous formaldehyde solution,
which comprises extracting as a 0.8 mol side stream, adding this to a
raw material gas, and reacting at a temperature of 580 to 680 ° C.
Description
translated from Japanese
DETAILED
DESCRIPTION OF THE INVENTION 1) Field of Industrial Application The
present invention relates to a method for producing a formaldehyde
aqueous solution having a low methanol content by catalytically
reacting a raw material gas containing methanol, air and water on a
silver catalyst.
2) Conventional technology As a method for
producing formaldehyde by oxidative dehydrogenation of methanol, a raw
material methanol and air were further obtained by reacting a raw
material gas obtained by adding steam and waste gas if necessary on a
silver catalyst. It is common to recover the reaction heat from the
reaction gas with a boiler, if necessary, and then introduce it into a
water absorption tower to recover formaldehyde as an aqueous solution.
In this case, since methanol is used in excess of air, unreacted
residual methanol is generally mixed in the obtained formaldehyde. The
residual methanol itself contributes to the stabilizing effect of the
formaldehyde solution, but the excessive presence of methanol is
wasteful, and in recent years, it has been required to produce an
aqueous formaldehyde solution having a low methanol content.
Therefore,
usually, a method is employed in which the amount of residual methanol
in the reaction product gas is reduced by increasing the air / methanol
molar ratio to about 1.8 to obtain formaldehyde having a low methanol
content. In this case, avoid the explosion range and suppress the
reaction temperature. Therefore, although steam is usually added to the
raw material gas, this steam remains in the reaction product gas and is
condensed in the absorption tower to reduce the concentration of the
product formaldehyde aqueous solution. Therefore, the concentration of
the formaldehyde aqueous solution produced by this method is limited to
about 45% by weight.
On the other hand, as an effective means
for reducing the methanol content of the product formaldehyde aqueous
solution and increasing the formaldehyde concentration, there is a
so-called waste gas circulation method in which a part of the
absorption tower waste gas is added to the raw material gas. Is also a
practically feasible product The concentration of formaldehyde aqueous
solution is 55
Up to about wt%.
Further, when the air /
methanol ratio of the raw material gas is increased, the combustion
reaction of methanol and other side reactions tend to proceed and the
formaldehyde selectivity tends to be lowered. Therefore, it is
preferable to make the air / methanol ratio as low as possible.
3)
Problems to be Solved by the Invention In order to solve the
above-mentioned drawbacks, the present invention has an air / methanol
molar ratio of the raw material gas of 1.5 to 1 when adding only steam
to the raw material gas. About 6 or about 1.6 to 1.8 when waste gas is
added to the raw material gas, and a formaldehyde aqueous solution
having a low methanol content and a high formaldehyde concentration
while reacting under milder conditions than conventional methods. To
provide a method of manufacturing.
4) Means for solving the
problem That is, in the present invention, a raw material gas
containing methanol, air and steam is subjected to a catalytic reaction
on a silver catalyst, and the obtained reaction product gas is
contacted with water to remove formaldehyde in the product gas. Absorb
in water, formaldehyde concentration 37 ~ 6 from the bottom of the
absorption tower
In a method for producing a 0% by weight
formaldehyde solution, water in an amount corresponding to water vapor
added to a raw material gas,
Add the total amount of water necessary
for diluting the product formaldehyde solution from the top of the
absorption tower as absorbed water, and from the upper stage of the
absorption tower, methanol concentration 0.1-3.0% by weight,
formaldehyde concentration 0.1-. This is a method of producing
formaldehyde by extracting an aqueous solution having a composition of
1.0% by weight as a side stream in an amount corresponding to water
vapor added to a raw material gas, adding this to the raw material gas
and reacting them.
5) Operation The raw material gas in the
present invention contains methanol, air and water vapor, and if
necessary, an inert gas such as a waste gas after the recovery of
formaldehyde can be added to the reaction.
The composition of the source gas is methanol 1 if no waste gas is added.
Empty 1.5-2.0 mol per mol, preferably 1.6-
It
is 1.8 moles, steam is 0.2 to 0.8 moles, and preferably 0.4 to 0.6
moles. When a waste gas is added, the empty space is 1.6 to 2.2 mol,
preferably 1.8 to 2.0 mol, and water vapor is 0.2 to 0.6 mol,
preferably 0.2 to 0. 5 mol, waste gas 0.2 to 2.0 mol, preferably 0.4 to
1.5 mol.
A raw material gas having such a composition is
introduced onto an ordinary catalyst for producing formaldehyde such as
electrolytic silver, and the temperature is 580 to 680 ° C., preferably
620 to 650 ° C., and the linear velocity is 0.8 to 2.0 m / se.
c, preferably 1.0 to 1.5 m / sec.
The reaction product gas obtained was formaldehyde 15-25.
%, Temperature 580-6 containing 0.2-2.0% methanol
It
is a high temperature gas of 80 ° C., and therefore, it is usually
passed through a multi-tube boiler installed directly below the reactor
to obtain a temperature of 120-
After cooling to 160 ° C, it is introduced into an absorption tower.
The
absorption tower is divided into three parts, the upper part, the
middle part and the lower part, and the upper part is the plate tower,
the middle part and the lower part are the packed towers. Water is
supplied from the top of the tower and formaldehyde in the reaction
product gas introduced from the bottom of the tower is absorbed. In the
packed towers in the middle and lower parts of the tower, the absorbed
water is withdrawn from the bottom of the tower to the outside as a
side stream, cooled, and then circulated again to the top of each
tower. Due to such external cooling, the temperature of the lower
packed tower is 60 to 80 ° C, and the temperature of the middle packed
tower is 20 to 30 ° C.
Kept at ℃. As a result, most of the
formaldehyde and part of the methanol are absorbed and condensed in the
lower packed column, and almost all of the formaldehyde and half of the
tanol are absorbed in the middle packed column.
From the top of
the upper tray tower, which is the top layer of the absorption tower,
the amount of water necessary for diluting the aqueous formaldehyde
solution that is withdrawn from the bottom of the tower as a product is
usually introduced as absorbed water. 600-2000 ppm formaldehyde in the
overhead gas released, 1
500-5000ppm methanol and methyl formate 7
A
loss of 0.00 to 3000 ppm is included. In the present invention, in
addition to the amount of water necessary for diluting the product
formaldehyde aqueous solution from the top of the plate tower, water is
added in an amount corresponding to the water added to the raw material
gas, and the upper plate column (total plate number 10 to 10). 25
stages) in the middle part (5 to 20 stages from the top of the column),
where the concentration of methanol is 0.1 to 3.0 wt% and the
concentration of formaldehyde is 0.1 to 1.0 wt% An amount equivalent to
the amount of water to be added is withdrawn as a sidestream, and this
is added to the raw material gas and reacted. Therefore, the amount of
water added from the top of the absorption tower is 2 to 5 times that
of the usual method, and accordingly, the content of formaldehyde,
methanol, methyl formate, etc. in the waste gas discharged from the top
of the absorption tower is remarkable. Decrease. Further, the side
stream extracted from the upper tray column contains 1 to 4 times,
especially 2 to 3 times by weight, methanol of formaldehyde, and the
addition of this to the raw material gas improves the methanol unit
consumption. And methanol is extracted as a sidestream, the amount of
methanol mixed in the product formaldehyde aqueous solution is reduced,
and it is possible to obtain a formaldehyde solution having a low
methanol content despite the reaction under methanol-rich reaction
conditions. .
The product formaldehyde solution obtained by the
present invention has a formaldehyde concentration of 37 to 60% by
weight, preferably 45 to
60 wt%, methanol concentration 0.5-3.0 wt%,
preferably 0.5-1.0 wt%, the amount of formic acid by-produced at this
time is 100 wtppm or less, usually about 50-60 wtppm Is. The water
extracted as a sidestream is heated to 60 to 80 ° C. by a heat
exchanger and is contacted with the raw material air to evaporate to
form a raw material gas.
6) Effect of the Invention According to
the present invention, the amount of absorbed water introduced from the
top of the absorption tower is larger than that in the usual method, so
that unabsorbed components in the waste gas are reduced,
Not only
can the unit consumption of methanol be improved by that much, but it
is also possible to react under mild reaction conditions by adopting
methanol-rich reaction conditions on the premise of recovery of
residual methanol. This also leads to the advantage that the amount of
water vapor to be mixed can be reduced, and the effect is extremely
large.
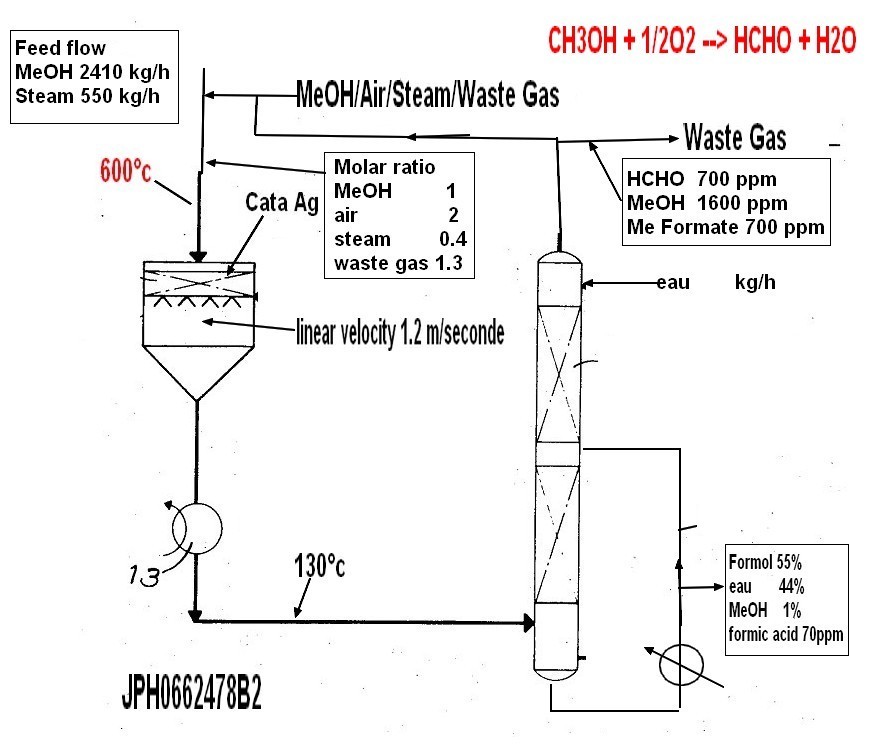
7) Example Example-1 In FIG. 1, 2410 kg / hr of methanol was introduced into 1 from FIG. Also from 3 air 3050 Nm 3 / hr
Is introduced into the humidifier 4 and extracted from 5 and the heat exchanger 6
Countercurrent
contact with 600 kg / hr of flowing water on the absorption tower side
heated to ℃. The sidestream water contained 2% by weight of methanol.
Humidified water is extracted from the bottom of the tower, and the
temperature is 65 ° C and 80%.
It was circulated at a flow rate of m 3 / hr. Air temperature at the humidifier outlet is 63
C.,
and the amount of humidification is adjusted by keeping this
temperature constant. The heated methanol vapor and air are mixed and
further enter reactor 8 with the waste gas from 7. The molar ratio of
methanol: air: steam: waste gas at the reactor inlet is 1: 1.8: 0.4:
1.3. A silver catalyst is held in the reactor and reacted at a reaction
temperature of 620 ° C. to form formaldehyde. The reaction product gas
exchanges heat with pressurized water by a waste heat boiler attached
to the lower part of the reactor and is cooled to 120 ° C, then enters
the bottom of the series column lower packed column 9 and
countercurrently flows with circulating water at 60 ° C of 10 140 m 3 /
hr. Contact. Most of the formaldehyde and part of the methanol are
absorbed here, and the residual gas is further circulated in the middle
packed column 11 at a temperature of 30 ° C 12 140 m 3
In
countercurrent contact with / hr, almost all of formaldehyde is
absorbed. Further, the unabsorbed gas is led to the upper tray tower 13,
In
countercurrent contact with 700 kg / hr of absorbed water having a
temperature of 20 ° C. introduced from the top, methanol and
formaldehyde are completely absorbed. The input gas extracted from the
top of the tower is formaldehyde 100ppm, methanol 300ppm, methyl
formate 400.
It only contained ppm. The product formaldehyde
solution was obtained at a rate of 3650 kg / hr from 15, the
formaldehyde concentration was 55% by weight, and the methanol
concentration was 1.
It was 0% by weight and formic acid content was 50 ppm by weight.
Example-2
As shown in FIG. 2, the waste gas 7 was introduced into the humidifier
4 together with air to increase the amount of humidification. The
composition of the raw material gas obtained as a result is methanol:
air: steam: waste gas = 1: 1.8: 0.6:
1.3.
The reactor
temperature was maintained at 610 ° C. The operating conditions of the
absorption tower are almost the same as in Example 1, but the amount of
absorbed water from the top of the absorption tower is 1000 kg / hr,
and the side-stream withdrawal amount is 900 kg.
/ Hr. The product
formaldehyde solution was obtained at the rate of 3950 kg / hr, the
formaldehyde concentration was 51% by weight, the methanol was 0.7% by
weight, the formic acid content was 50% by weight, and the waste gas
contained 80% formaldehyde and 25% methanol.
It contained 0 ppm and 350 ppm of methyl formate.
Example-3
In FIG. 1, 2250 kg / hr of methanol was introduced into the evaporator
2 from 1 and made into a gaseous state. In addition, air from 3 is 2530
Nm 3 / hr
Is introduced into the humidifier 4 and extracted from 5 and the heat exchanger 6
The
countercurrent contact of 900 kg / hr of flowing water on the
absorption tower side heated to ℃. This sidestream water contained 1.7%
by weight of methanol. The water from the humidifier is withdrawn from
the bottom of the tower and the temperature is 65 ° C.
Circulation was carried out at a flow rate of 0 m 3 / hr. Air temperature at the humidifier outlet is 6
It
is 2 ° C., and the amount of humidification is adjusted by keeping this
temperature constant. The heated methanol vapor and air are mixed and
enter the reactor 8 (waste gas is not mixed).
The molar ratio of
methanol: air: steam at the reactor inlet is 1: 1.6: 0.7. A silver
catalyst is held in the reactor and reacted at a reaction temperature
of 620 ° C. to form formaldehyde. The reaction product gas exchanges
heat with pressurized water in a waste heat boiler attached to the
lower part of the reactor, is cooled to 110 ° C., and then enters the
bottom part of the absorption tower lower packed column 9, and the
circulating water at 60 ° C. 10 1
Countercurrent contact with 40 m 3
/ hr. Most of the formaldehyde and part of the methanol are absorbed
here, and the residual gas is countercurrently contacted with the
circulating water of 12 140 m 3 / hr at 30 ° C in the middle packed
column 11 and almost all of the formaldehyde is absorbed. .
Further,
the unabsorbed gas is introduced into the upper tray column 13 and
comes into countercurrent contact with 1400 kg / hr of absorbed water
having a temperature of 20 ° C. introduced from the top, and methanol
and formaldehyde are completely absorbed. The waste gas extracted from
the top of the tower is formaldehyde 6
It contained only 0 ppm, 200
ppm methanol, and 300 ppm methyl formate. The product formaldehyde
solution was obtained from 15 at a rate of 3890 kg / hr, the
formaldehyde concentration was 47.6% by weight, and the methanol
concentration was 3.4.
% By weight, and the formic acid content was 50 ppm by weight.
Comparative
Example 1 In FIG. 1, there is no side stream 5 and humidifier 4, and
the steam added to the raw material gas was mixed with other raw
material gas (methanol, air, waste gas) in front of the reactor 8.
That
is, 2410 kg / hr of methanol is introduced from 1 into the evaporator 2
and made into a gaseous state. In addition, 3 3 Nm 3 / hr of air was
introduced from 3, and the heated methanol vapor and air were mixed,
Add
550 kg / hr of steam. The mixed gas also enters reactor 8 along with
waste gas from 7.
The molar ratio of methanol: air: steam: waste gas at
the reactor inlet is 1: 2.0: 0.4: 1.3.
A silver catalyst is
retained in the reactor and reacts at a reaction rate of 650 ° C to
form formaldehyde. The reaction product gas exchanges heat with
pressurized water in a waste heat boiler attached to the bottom of the
reactor and is cooled to 130 ° C, then enters the bottom of the
absorption tower lower packed tower 9
Countercurrent contact with
circulating water 10 (140m 3 / hr) at ℃. Most of the formaldehyde and a
part of the methanol are absorbed here, and the residual gas is brought
into countercurrent contact with the circulating water 12 (140 m 3 /
hr) at 30 ° C in the middle packed column 11, and the unabsorbed gas is
further absorbed in the upper plate column. Led to 13,
Most of the
formaldehyde is absorbed by making countercurrent contact with 100 kg /
hr of absorbed water at a temperature of 20 ° C, which is introduced
from the top.
The waste gas extracted from the top of the tower is formaldehyde 700
ppm,
methanol 1600 ppm, methyl formate 700 ppm. 3610 kg / hr of product
formaldehyde solution was obtained, and the product formaldehyde
concentration was 55% by weight.
The methanol concentration was 1.0% by weight, and the formic acid content was 70 ppm by weight.
COMPARATIVE
EXAMPLE 2 In Comparative Example 1, 3050 Nm 3 / hr of air was
introduced from 3 . The molar ratio of methanol: air: steam: waste gas
at the reactor inlet is 1: 1.8: 0.4: 1.3, and the reaction temperature
in the reactor is 630 ° C.
The waste gas extracted from the top of the tower is formaldehyde 670
ppm,
methanol 1700 ppm, methyl formate 720 ppm. A product formaldehyde
solution of 3600 kg / hr was obtained, where the product formaldehyde
concentration was 54.6% by weight, the methanol concentration was 1.2%
by weight, and the formic acid content was 65%.
It was ppm by weight.
[Brief description of drawings]
Publication number
Priority date
Publication date
Assignee
Title
DE2022818B2
*
1970-05-11
1976-06-16
Basf Ag, 6700 Ludwigshafen
PROCESS FOR PRODUCING FORMALDEHYDE
IT1010299B
*
1973-05-11
1977-01-10
Basf Ag
PROCESS FOR THE PREPARATION OF FORMALDEHYDE
DE2444586C3
*
1974-09-18
1986-07-10
Basf Ag, 6700 Ludwigshafen
Process for the preparation of concentrated, aqueous solutions of formaldehyde
US4383123A
*
1981-10-08
1983-05-10
Monsanto Company
Manufacture of aqueous formaldehyde
US4454354A
*
1982-08-02
1984-06-12
Monsanto Company
Manufacture of aqueous formaldehyde
* Cited by examiner, † Cited by third party
Publication number
Priority date
Publication date
Assignee
Title
US4990685A
*
1988-07-19
1991-02-05
Bayer Aktiengesellschaft
Process for the preparation of aqueous formaldehyde solutions
ES2103193B1
*
1995-05-16
1998-04-01
Patentes Novedades Sa
PROCEDURE FOR THE CONTINUOUS PREPARATION OF AQUEOUS FORMALDEHYDE SOLUTIONS.
AU2001240390A1
*
2000-03-06
2001-09-17
Woodland Chemical Systems Inc.
A process for converting cellulosic material into liquid hydrocarbons
DE102008059701A1
*
2008-11-29
2010-06-02
Bayer Materialscience Ag
Process for the preparation of aqueous formaldehyde solutions
DE102014011476A1
*
2014-07-31
2015-11-12
Basf Se
Process for the preparation of acrylic acid from methanol and acetic acid
AT516530B1
*
2014-11-20
2018-02-15
Johnson Matthey Plc
Process and apparatus for the preparation of an aqueous solution of formaldehyde
WO2020027133A1
*
2018-07-30
2020-02-06
株式会社シーライブ
Composition for sterilization and nucleic acid degradation
KR102104920B1
*
2020-02-05
2020-04-27
박근식
Method for producing formaldehyde aqueous solution
CN113200827A
*
2021-05-19
2021-08-03
宁夏华业精细化学科技有限公司
Paraformaldehyde production process
WO2024166931A1
*
2023-02-08
2024-08-15
三菱瓦斯化学株式会社
Formaldehyde absorption system, absorption method, and method for designing absorption system
* Cited by examiner, † Cited by third party, ‡ Family to family citation
**************************************************************************************************
US4390730A
*
1981-07-27
1983-06-28
Celanese Corporation
Formaldehyde production
Abstract
Lead-silver
catalysts have been found to be useful in the production of
formaldehyde by oxidative dehydrogenation of methanol vapor with an
oxygen-containing gas at elevated temperatures.
BACKGROUND OF THE INVENTION
Silver
catalysts in the form of granules, gauze, wire turnings, crystals, and
the like have been used for many years to produce formaldehyde by the
oxidative dehydrogenation of methanol. Silver crystals are especially
suitable for this purpose, since they are very selective and have
little tendency to promote side reactions and the formation of
by-products under reaction conditions which permit high overall yields.
Numerous
prior art patents and publications describe the addition of small
amounts of promoters to silver catalysts used in the production of
formaldehyde from methanol. For example, U.S. Pat. No. 1,937,381,
issued to Bond et al on Nov. 28, 1933 and assigned to du Pont,
describes silver crystal oxidation catalysts containing promoters such
as oxides of tungsten, vanadium, cerium, thorium, molybdenum, chromium,
aluminum and zinc. Silver-cadmium alloy catalysts for the oxidative
dehydrogenation of methanol are shown in U.S. Pat. No. 3,334,143,
issued to Stiles on Aug. 1, 1960 and also assigned to du Pont. Silver
containing up to 10% of an oxide of barium, strontium or calcium and up
to 8% of an oxide of indium are taught as methanol oxidative
dehydrogenation catalysts in U.S. Pat. No. 4,045,369, issued to
Cantaluppi on Aug. 30, 1977 and assigned to S.A.E.S. Getters S.p.A.
None of these patents suggest the use of lead in combination with
silver as a methanol oxidative dehydrogenation catalyst.
Two
literature articles from the Soviet Union, each entitled "Catalytic
Properties of Silver Alloys in the Conversion of Methanol into
Formaldehyde", also disclose various additives alloyed with silver for
the oxidation of methanol to formaldehyde. The first is an abstract of
The Russian Journal of Physical Chemistry, 45 (10), 1971 p. 1524. It
discloses as methanol oxidative dehydrogenation catalysts silver alloys
of aluminum, magnesium, copper, zinc, gallium, germanium, selenium,
cadmium, indium, tin, antimony, tellurium and bismuth. The other
publication is an article from Tekh. Progr. Dostizh Nauki Khim, Prom.
1973, p. 191-5 abstracted in Chemical Abstracts Vol. 81, 68971, 1974.
It describes the same silver alloys as the first abstract except that
the selenium and antimony alloys are not included. There is no mention
of lead-silver catalysts in these articles. Of specific interest,
however, is the description of the attempt to improve silver catalysts
by adding tin and germanium (or the same group in the Periodic Table as
lead) to improve the oxidative dehydrogenation of methanol to
formaldehyde. Both of these additives to silver gave exceptionally poor
results for formaldehyde production, compared to the use of silver
alone.
A paper by Schwab entitled "Metal Electrons and Catalysts" in
the The Transactions of the Faraday Society Vol. 42, 1946 p. 689-697,
describes heterogeneous and homogeneous alloys of lead-silver, among
other alloys. However, these catalysts were used to dehydrogenate
formic acid to hydrogen and carbon dioxide, a reaction substantially
different from the oxidative dehydrogenation of methanol to
formaldehyde.
Another prior art patent, U.S. Pat. No. 3,948,997,
issued Apr. 6, 1976 to Howe et al, describes a process for the vapor
phase oxidation of α,β-diols such as ethylene glycol to α,β-diones such
as glyoxal at elevated temperatures in the presence of a catalyst
containing as essential constituents, one or more metals of Group Ib of
the Periodic Table comprising copper, silver and gold, and one or more
elements from Group IVa, comprising germanium, tin and lead, and Group
Va, comprising nitrogen, phosphorus, arsenic, antimony and bismuth.
However, there is no specific disclosure in this patent of a
lead-silver catalyst, per se, nor is there any suggestion that any of
the catalysts disclosed generically or specifically, could be used for
the oxidative dehydrogenation of methanol to formaldehyde.
DETAILED DESCRIPTION OF THE INVENTION
The
lead-silver catalysts used in the process of the present invention are
readily prepared by impregnating lead onto silver. Preferably, the
silver base used is silver crystals which are somewhat porous or
irregular, e.g., silver crystals having particle sizes ranging from
about 8 to about 40 mesh U.S. screen size (i.e. particles which will
pass through a 8 mesh screen but which will be retained on a 40 mesh
screen). A small amount of silver crystals having a mesh size larger
than 8 mesh, i.e., up to about 10 weight percent of the total crystals,
can be tolerated in the methanol conversion, but if the amount of large
silver particles becomes excessive, the contact of methanol and oxygen
with the silver crystals will be significantly decreased, resulting in
lessened formaldehyde production. On the other hand, a small amount of
silver crystals smaller than 40 mesh (again up to about 10 weight
percent of the total catalyst) can be used in the methanol reaction.
However, if a significant amount of smaller particles are present, an
undesirable increase in the pressure drop across the catalyst bed may
be observed. Particularly preferred are silver crystals having particle
sizes ranging from about 20 to about 30 mesh (U.S. screen size).
One
technique for preparing the catalysts of this invention involves
impregnating silver crystals with a decomposable salt of lead, such as
lead acetate, lead nitrate, or the like, and then decomposing the lead
salt, for example by heat. Lead can also be applied to silver crystals
by immersing the crystals in an organic or aqueous solution of a
soluble lead salt and evaporating the solvent, preferably while
stirring to obtain a more uniform distribution of lead on the silver
crystals. Also a suspension or colloidal solution of a lead compound,
prepared by any of the ordinary methods, may be flocculated while in
contact with silver crystals to give a lead-silver catalyst.
The
catalysts used in the process of this invention comprise silver and
lead. The amount of lead in the catalyst can range from about 100 to
about 150,000 parts per million, based on the total catalyst, and
silver can comprise the remainder of the catalyst. The weight ratio of
lead to silver on this basis can range from about 0.0001 to about 0.15.
The preferred amount of lead in these catalysts can range from about
1000 to about 7000 parts per million, based on the total catalyst, with
silver comprising the remainder of the catalyst. The preferred weight
ratio of lead to silver can range from about 0.001 to about 0.007.
Lead-silver
catalyst can also be prepared by depositing lead and silver on selected
catalyst supports, such as silicon carbide or α-alumina, which do not
detrimentally affect oxidative dehydrogenation of methanol to
formaldehyde under the reaction conditions of the present invention.
Such catalysts and processing conditions are described in copending
application U.S. Ser. No. 287,385, filed July 27, 1981 in the names of
H. R. Gerberich and E. T. Smith assigned to Celanese Corporation and
filed concurrently with this application.
The process of this
invention can be carried out in any conventional single stage or
multiple stage methanol oxidation reactor at elevated temperatures.
Individual reactors require facilities to hold a sufficient amount of
oxidative dehydrogenation catalyst and to permit the methanol-oxygen
mixture to pass over the catalyst to accomplish oxidative
dehydrogenation. Downstream facilities to recover the formaldehyde
product, normally in aqueous solution, are also required.
In
carrying out the process of this invention, a feed mix of methanol and
an oxygen-containing stream, such as pure oxygen, a mixture of oxygen
and nitrogen, air, or other oxygen sources, i.e., one containing about
5 mol percent to about 100 mol percent of oxygen, is passed into a
reactor containing catalyst comprising lead and silver and reacted at a
temperature in the range from about 500° C. to about 700° C.,
preferably about 550° C. to about 650° C. Diluents such as steam and
nitrogen, if desired, can be added to the methanol-oxygen mixture in
amounts ranging from about 0.1 to about 10 mole of diluent per mole
methanol in the feed, and preferably from about 0.75 to about 3 mole of
dilute per mole methanol in the feed. The mole ratio of oxygen to
methanol in the feed can range from about 0.15 to about 0.8, and
preferably from about 0.2 to about 0.5. The space velocity of the feed
entering the reactor generally will be maintained at from about 10 to
about 150 reciprocal seconds, and preferably at from about 25 to about
80 reciprocal seconds.
Single stage operations, such as described
above, although quite widely used to produce formaldehyde, suffer from
the disadvantage that rather high amounts of unconverted methanol are
contained in the product emerging from the catalyst bed. The presence
of methanol in the exiting formaldehyde solution is undesirable since
the methanol, generally, must be separated from the formaldehyde using
expensive distillation facilities. However, the need for a separation
step can be avoided by using a second oxidation stage of reaction. When
carrying out a second oxidation, the effluent gases from the first
stage reactor can be cooled, preferably below about 250° C., and mixed
with an additional oxygen-containing stream, such as air. The use of
such a two stage oxidation process is described in U.S. Pat. Nos.
2,462,413; 3,959,383; 3,987,107 and 4,076,754, among others. The
effluent gas-oxygen mixture is then passed through a second stage
catalytic oxidative dehydrogenation reactor containing sufficient
catalyst to convert substantially all of the remaining unreacted
methanol to formaldehyde. Temperatures in the range from about 550° C.
to about 700° C., and preferably from about 600° C. to about 675° C.,
generally will be employed, while the space velocity of the gas in the
second stage oxidation reactor generally will be maintained in the
range of from about 10 to about 200 reciprocal seconds and preferably
from about 30 to about 100 reciprocal seconds.
Any catalyst for the
conversion of methanol to formaldehyde, and preferably a
silver-containing catalyst, can be used in the second oxidation stage.
Lead and silver catalysts, such as those used in the first stage
oxidation reaction described above, can be used in the second stage as
well. Conventionally used silver crystals, with or without other
additives, can also be used.
The effluent gas emerging from the
second stage can be passed through a cooler and then passed into the
base of an absorber column. A stream of water may be introduced at the
top of the absorber column in order to adjust the formaldehyde
concentration in the aqueous formaldehyde product which is removed from
the bottom of the column. The non-condensable gases entering the
absorber are vented at the top of the column to an incinerator or to
the atmosphere.
The advantages of the invention can be seen by reference to the following examples
EXAMPLE 1
The
unpromoted silver used in this and the following examples as a catalyst
per se, as well as a base for the promoted catalysts of the present
invention, was 20 to 30 U.S. screen mesh size silver crystals,
electrolytic grade, 99.9% purity. To produce the promoted catalysts, an
appropriate amount of lead acetate, antimony di-tartrate, or bismuth
nitrate was impregnated on the silver crystals.
This was
accomplished by first adding a solution of the desired metal salt to
the silver crystals using an amount of solution just sufficient to
cover the crystals. The liquid was then removed under vacuum, as a
vapor, by heating. As an illustration, to prepare a silver catalyst
containing 10,000 parts per million lead, lead acetate [Pb(OAc)2.3H2
O)] in the amount of 0.46 gram was dissolved in demineralized water to
make 5.8 ml of solution. This solution was poured onto 25 grams of
silver crystals. The water solvent was then removed under vacuum at
100° C.
In preparing the antimony-containing catalysts, antimony
di-tartrate, which is soluble in demineralized water, was poured on
silver catalysts and the aqueous solvent removed by vaporization under
vacuum at 100° C. In preparing the bismuth-containing catalysts,
bismuth nitrate, dissolved in methanol containing a minor amount of
concentrated nitric acid added to aid in the solubilization, was poured
on silver crystals and the excess methanol removed by vaporization
under vacuum at 100° C. After the catalysts were prepared, they were
placed in the catalyst bed of the methanol oxidation unit.
EXAMPLES 2-16
The
methanol oxidation unit used for these examples was an insulated,
cylindrical reactor made of 316 stainless steel which is 7 inches long
and has an internal diameter of 7/8 inch. In each run the reactor
contained 17 grams of unpromoted silver catalyst. The catalyst bed was
0.5 inch deep. A thermocouple inserted into the catalyst bed was used
to measure the reaction temperature. Air [7605 cc (STP)/min] was
sparged into a heated vessel of liquid methanol. The gas leaving this
vaporizer contains air to methanol mole ratio of 1.15 to 1.24. This
vapor stream was mixed with a flow of pure nitrogen (1949 cc/min) and
heated to 125° C. to avoid condensation. The mixture was fed to the
methanol oxidation unit described above. Reaction was initiated by
heating the catalyst bed with an electrical resistance winding which is
on the external surface of the reactor. As soon as the methanol
conversion reaction occurred as indicated by a sudden rise in
temperature to 450° C. or above the timing of the run was begun. The
conversions of methanol, which ranged from about 69 to about 76
percent, were collected by keeping the air and thus the oxygen in the
feed stream constant and varying the oxygen-methanol ratio by
controlling the methanol in the stream, with higher oxygen-methanol
ratios yielding higher methanol conversions. Once the reaction, which
is exothermic, was initiated, the temperature was permitted to reach
its own level, with no external heat being added to the reaction and no
heat being deliberately absorbed by heat exchangers while the reaction
is continuing, although an undetermined amount of heat may of course
have escaped into the surroundings through the reactor walls. The
product stream is analyzed by gas chromatography for mole percent
nitrogen, oxygen, methanol, carbon dioxide, carbon monoxide, hydrogen
and methyl formate. Data were collected for the period of 5 to 20 hours
after initiation of the reaction. The conditions of the reaction were:
catalyst temperature-545°-612° C.
reaction pressure-5.8 psig
oxygen conversion-99.5 percent
space velocity-51 sec-1
Table
I sets out the results of the methanol oxidative dehydrogenation to
formaldehyde using the unpromoted silver crystals for comparison with
the promoted catalysts under the conditions set forth above. The table
indicates catalyst temperatures used in the reaction, length of run,
conversions of methanol to total products, and the efficiencies of
converted methanol to carbon dioxide (CO2), methyl formate (MeFo) and
formaldehyde (HCHO).
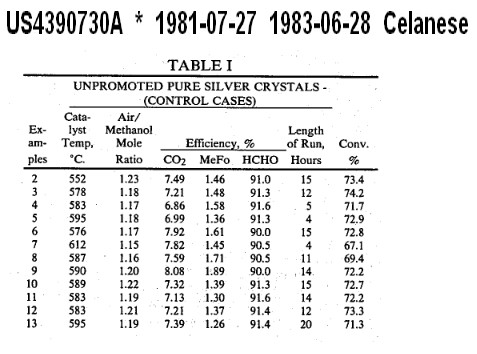
*************************************************************************************************
CN113200827A
*
2021-05-19
2021-08-03
宁夏华业精细化学科技有限公司
Paraformaldehyde production processAbstract
The
invention discloses a production process of paraformaldehyde, which
comprises the following steps: comprises a formaldehyde evaporation
process, a methanol oxidation process, a formaldehyde absorption
process, a formaldehyde concentration process and a paraformaldehyde
drying process. The invention belongs to the technical field of
paraformaldehyde production, and particularly relates to a
paraformaldehyde production process, which is characterized in that
methanol and air are used as raw materials, the production process
comprises the working procedures of catalytic oxidation, absorption and
the like, the methanol is subjected to catalytic dehydrogenation to
obtain formaldehyde, the formaldehyde is absorbed by water to obtain a
37% formaldehyde solution, the formaldehyde solution is concentrated,
and a vacuum rake dryer is used for drying and producing the
formaldehyde solution to obtain a paraformaldehyde finished product.
Description
Paraformaldehyde production process
Technical Field
The
invention belongs to the technical field of paraformaldehyde
production, and particularly relates to a paraformaldehyde production
process.
Background
Paraformaldehyde is a product produced by
dehydration, concentration, drying and polymerization of an aqueous
formaldehyde solution, is a mixture of formaldehyde molecules, namely
polyoxymethylene glycol HO (CH2O) nH and the like, and is a linear
polymer important in chemical engineering.
Disclosure of Invention
In order to solve the problems, the invention provides a paraformaldehyde production process.
In
order to realize the functions, the technical scheme adopted by the
invention is as follows: a production process of paraformaldehyde
comprises the following steps:
1) a methanol evaporation process:
air is sent into an air washing tower by an air fan, the air enters a
methanol evaporator after being washed by water, methanol is sent into
the methanol evaporator from a tank area by a pump, the methanol
feeding flow is interlocked with the air feeding flow, the feeding
proportion is controlled, the formaldehyde liquid generated by the No.
1 absorption tower is used as a heat source to exchange heat with the
methanol liquid in the methanol evaporator, so that the temperature of
the methanol liquid is raised, and then the methanol gas is generated
by bubbling through the air;
2) a methanol oxidation step:
introducing a certain amount of water vapor of 0.4MPa and 152 ℃
supplied by an oxidizer steam drum at the top of a methanol evaporator,
mixing the water vapor with methanol gas, feeding part of tail gas
generated by subsequent reaction into the methanol evaporator through a
tail gas fan in proportion to air so as to utilize the heat energy of
the tail gas to heat the methanol gas, heating the mixed gas consisting
of the methanol gas, the air, the steam and the tail gas containing a
small amount of methanol gas to 110 ℃ through pyrogen steam, and
sending the mixed gas to a subsequent oxidation section;
3) wherein, the methanol oxidation process comprises the following reaction steps:
CH3OH+1/2O2→CH2O+H2O△H=+156.557kJ/mol CH3OH→
CH2O+H2△H=-85.27kJ/mol
side reaction:
CH3OH+O2→CO+2H2O CH3OH+3/2O2→CO2+2H2O CH2O+
1/2O2→HCOOH HCOOH→CO+H2O;
the
mixed gas enters an oxidizer at 110 ℃, is subjected to oxidation
reaction under the catalysis of an electrolytic silver catalyst at
580-650 ℃ to generate formaldehyde gas, emits a large amount of heat,
soft water is introduced into a jacket of the oxidizer to remove the
reaction heat, the water is converted into steam, the steam enters a
steam pocket of the oxidizer, the steam is supplied for production
between the oxidizer and the oxidizer through a steam distributor, the
rest of the steam is introduced into a steam pipe network of a plant
area, and meanwhile, the formaldehyde gas at the outlet of the oxidizer
is cooled to about 180 ℃;
4) a formaldehyde absorption procedure:
the formaldehyde gas generated in the methanol oxidation process is
sequentially sent into a 1# absorption tower and a 2# absorption tower
for water spraying absorption, tail gas is led out from the top of the
2# absorption tower and is sent to a tail gas boiler, fresh water is
supplemented from the top of the 2# absorption tower and is in
countercurrent contact with synthesis gas to absorb formaldehyde, a
dilute formaldehyde solution extracted from the bottom of the 2#
absorption tower is pumped into the 1# absorption tower and is in
countercurrent contact with the synthesis gas entering the 1#
absorption tower, and the formaldehyde solution (with the concentration
of about 37%) is extracted from the bottom of the 1# absorption tower
and is sent to a formaldehyde intermediate tank for temporary storage.
5)
A formaldehyde concentration procedure: conveying 37% of formaldehyde
solution from a formaldehyde intermediate tank into a first-effect
evaporator, heating to 80 ℃ under negative pressure for evaporation
concentration, mixing gas and liquid, keeping the temperature of 80 ℃,
feeding the mixture into a first-effect separator, feeding water vapor
from the upper side of the first-effect separator into a vacuum
absorption tower for absorption, conveying 55% of concentrated
formaldehyde at the bottom of the first-effect separator into a
concentrated formaldehyde kettle, and keeping the temperature of the
concentrated formaldehyde at 80 ℃ by using a 95 ℃ hot water jacket for
heat tracing through a pipeline between the first-effect separator and
a dryer and tank equipment so as to prevent the concentrated
formaldehyde from self-polymerization;
6) and a paraformaldehyde drying procedure:
the formaldehyde polymerization equation is as follows: nHCHO → (CH2O) n (n ═ 8 to 100)
55%
concentrated formaldehyde circularly conveyed by a concentrated
formaldehyde kettle is conveyed to a vacuum rake dryer, 50% liquid
caustic soda is quantitatively mixed in a liquid caustic soda metering
tank, and the liquid caustic soda is pumped into the vacuum rake dryer
by a liquid caustic soda feeding pump to catalyze formaldehyde
polymerization, so that the formaldehyde polymerization speed is
accelerated: introducing 151 ℃ steam into a jacket of the vacuum rake
dryer to control the reaction temperature of the materials to be 80 ℃,
simultaneously vacuumizing to ensure the negative pressure of the
equipment, feeding concentrated formaldehyde and liquid caustic soda
into the vacuum rake dryer for polymerization and drying, feeding the
dried product into a paraformaldehyde packaging bin, packaging, and
conveying to a polyformaldehyde shed area for storage and sale;
7)
the tail gas burning contains combustible substances such as H2, CH2O,
CH3OH, CO and HCOOH in unabsorbed gas (namely tail gas) that comes out
from the top of the 2# absorption tower, part of tail gas is recycled,
the tail gas is sent into the methanol evaporator through the tail gas
fan to participate in the reaction, the rest tail gas is sent into the
tail gas boiler to burn, the tail gas burning generates a large amount
of heat, soft water is introduced into the coil pipe of the tail gas
processor, the soft water enters the tail gas steam pocket after heat
exchange, the generated steam is merged into the steam pipe network of
the plant area, and the waste gas generated after the tail gas burning
is emptied through the exhaust funnel.
Further, the alcohol feeding
flow rate and the air feeding flow rate are interlocked in the step 1),
and the feeding proportion is controlled, so that the feeding
oxygen-alcohol ratio is kept between 0.39 and 0.45.
Further, the
ratio of the oxygen alcohol steam ternary gas in the step 2) is as
follows: oxygen: methanol: steam 0.39: 1: 0.25-0.45: 1: 5.
the
invention adopts the structure to obtain the following beneficial
effects: the production process of the paraformaldehyde provided by the
invention is simple to operate, compact in mechanism and reasonable in
design, and comprises the following steps: comprises a formaldehyde
evaporation process, a methanol oxidation process, a formaldehyde
absorption process, a formaldehyde concentration process and a
paraformaldehyde drying process. Methanol and air are used as raw
materials, the production process of the procedures of catalytic
oxidation, absorption and the like is carried out, the methanol is
subjected to catalytic dehydrogenation to obtain formaldehyde, the
formaldehyde is absorbed by water to obtain a 37% formaldehyde
solution, and the formaldehyde solution is concentrated and dried by a
vacuum rake dryer to obtain a paraformaldehyde finished product.
Detailed Description
Publication number
Priority date
Publication date
Assignee
Title
JPS60215644A
*
1984-04-12
1985-10-29
Mitsubishi Gas Chem Co Inc
Preparation of aqueous solution of formaldehyde
CN102757324A
*
2012-05-22
2012-10-31
山西阳煤丰喜肥业(集团)有限责任公司
Method for producing formaldehyde from methanol under oxygen-rich condition and utilizing formaldehyde exhaust gas
CN105218334A
*
2015-11-17
2016-01-06
安徽弘源化工科技有限公司
A kind of prepn. of formaldehyde
CN105218769A
*
2015-11-17
2016-01-06
安徽弘源化工科技有限公司
The technique of 50% concentration Formaldehyde Production paraformaldehyde
CN105294414A
*
2015-11-19
2016-02-03
安徽中源化工有限公司
Formaldehyde production system
CN105399612A
*
2015-11-19
2016-03-16
安徽中源化工有限公司
Technology for producing paraformaldehyde from formaldehyde with concentration of 37%
Publication
Publication Date
Title
CN100500550C
2009-06-17
Method of preparing hydrogen by reforming methanol-water steam
CN105566077B
2017-05-24
Process method for preparing polyoxymethylene dimethyl ethers
CN100506353C
2009-07-01
Techniques
of flue gas desulpurizing through catalytic oxidation method and
by-product polymerizing iron sulfate through catalytic method
CN110155953A
2019-08-23
A kind of processing low-concentration acid gas carries out the device and technique of sulphur recovery
CN107353188A
2017-11-17
A kind of method for preparing anhydrous gaseous formaldehyde
CN205556509U
2016-09-07
Preparation gathers methoxy dimethyl ether DMM3 -5's process units
CN107445809B
2023-05-12
Device and method for producing concentrated formaldehyde
CN104513144A
2015-04-15
Method of recycling methanol in formaldehyde production through silver method
CN209098538U
2019-07-12
A kind of flue gas recirculation formaldehyde production device
CN101185828B
2010-10-27
Waste gas treatment method in glassine production process
CN203947049U
2014-11-19
A kind of device of preparing formaldehyde
CN105777540A
2016-07-20
Energy-saving efficient isopropenyl acetate synthesis method
CN201770629U
2011-03-23
Device for preparing alcohol-free formaldehyde with high concentration
CN216703358U
2022-06-10
Methanol vaporizer of silver method formaldehyde production technology
CN101077855B
2011-12-07
Technique and device for continuously dehydrogenating and producing sodium oxalate by dehydrogenation reaction remaining heat
CN116855279A
2023-10-10
System and method for treating coal gas water circulation concentrated solution of fixed bed gasifier
CN109180445A
2019-01-11
A kind of formaldehyde production technology device and method
CN115160118A
2022-10-11
Closed formaldehyde production process flow
CN201495187U
2010-06-02
Methanol removing system of formaldehyde adsorption tower
********************************************************************************
CN107353188A
2017-11-17
A kind of method for preparing anhydrous gaseous formaldehyde
A kind of method for preparing anhydrous gaseous formaldehyde
Abstract
The
invention discloses a kind of method for preparing anhydrous gaseous
formaldehyde, methods described sequentially includes:(1) carry out
formaldehyde and prepare reaction;(2) formaldehyde in alcohol
absorption step (1) is used to prepare the product reacted;And (3) by
the product heats in previous step to 125 to 180 DEG C to discharge
anhydrous gaseous formaldehyde.By the present invention, anhydrous
gaseous formaldehyde can be directly obtained, and technique is simple,
flow is short, and more other anhydrous gaseous formaldehyde
preparation method energy consumptions are greatly reduced, and avoid
the participation of extra water, so as to which wastewater discharge
is also greatly decreased.
Background technology
Formaldehyde
is a kind of important Organic Ingredients in chemical field, and its
property is active, mainly as production agriculture The raw material
of the materials such as medicine glyphosate, phenolic resin, Lauxite,
polyacetal resin, melamine resin and centre Body, it is widely used in
coating and field of pesticides.
The method of industrial production
formaldehyde is very ripe at present, uses methanol oxidizing process
mostly, i.e., in silver, copper etc. In the presence of metallic
catalyst Oxidation of Methanol is to generate the method for
formaldehyde, here, in the oxidizing gas of generation All using water
come spray-absorption formaldehyde in absorption, so as to finally give
37%-40% formalin.
But required in the production process of many products using anhydrous formaldehyde,
such as resinae, special agricultural chemicals Class etc., and demand
is larger.Obtain anhydrous formaldehyde, it is necessary to which
presently commercially available formalin is entered Row distillation
operation, this will not only put into more considerable equipment,
operating cost, and formaldehyde can also be with water shape Into
azeotropic mixture, the difficulty of separation is further
increased.Or, it is desirable to it can also be adopted in anhydrous
reaction With paraformaldehyde, still, the preparation process of
paraformaldehyde is also required to formalin being concentrated by
evaporation, dried Deng can equally consume substantial amounts of
energy, this is not economic and environment-friendly enough.It also
proposed in recent years in catalyst In the presence of make methanol
direct dehydrogenation generation formaldehyde and hydrogen method, the
method reaction after do not generate water, can Directly obtain
anhydrous formaldehyde.However, the problem of methods described is
present is catalyst easily poisoning and inactivation, circulation
Utilization rate is poor, thus also only resides within laboratory
demonstration and improved stage, there is not yet large-scale
production Report.
Therefore, according to the current method by
producing formaldehyde by methanol oxidation, a kind of new production
nothing is developed The technique of water beetle aldehyd
According
to another implementation of the invention, the formaldehyde prepares
reaction and can also be natural gas oxidizing process Or methanol
dehydrogenation method etc..Wherein, the main reaction such as
following formula of the natural gas oxidizing process (namely for
methane oxidizing process) Shown in 2.
[formula 2]
CH4+O2→H2O+HCHO
Also,
in the natural gas oxidizing process, used catalyst is this area
catalytically oxidizing natural gas (methane) be made formaldehyde
custom catalystses, for example, MoO3/SiO2、V2O5/SiO2、Cr2O3/SiO2、
Fe-Mo-Co、Mo/ZrO2Deng catalyst, but the present invention is not limited
to this.It is further, since described natural Product in gas oxidizing
process also includes water, so the present invention's prepares the
method for anhydrous gaseous formaldehyde in step (2) (3) can also
further comprise the absorbent of gained in step (2) being evaporated
under reduced pressure between to remove moisture Process.
Wherein, the main reaction of the methanol dehydrogenation method is as shown in following formula 3.
[formula 3]
CH3OH→H2+HCHO
Also,
in the methanol dehydrogenation method, used catalyst is this area
catalysis methanol direct dehydrogenation So that the custom
catalystses of formaldehyde are made, for example,
Ag/SiO2-ZnO、Ag/SiO2The catalyst such as-MgO, but The present
invention is not limited to this.In addition, although the main
reaction of the methanol dehydrogenation method does not produce water,
but according to Need, the method for preparing anhydrous gaseous
formaldehyde of the invention also can be between step (2) and (3)
further Including the absorbent of gained in step (2) is evaporated
under reduced pressure with dewatered process.
In
the present invention, the product that the formaldehyde prepares
reaction be gas phase, and it refers to chemically reacting from
passing through Generate the derived gas-phase product mixture for
including formaldehyde, the gas-phase product mixture in the reactor of
formaldehyde May contain unreacted raw material (such as methanol,
oxygen, CO), reaction product (for example, formaldehyde, Water,
hydrogen etc.) and other foreign gases and/or side reaction product gas
etc., wherein the formaldehyde included can To generate hemiacetal with
alcohol in procedure described above (2), so as to be dissolved in
alcohol, meanwhile, alcohol is again The good solvent of formaldehyde,
thus the alcohol not still condensing agent of formaldehyde, or the
solvent of formaldehyde.
Therefore,
according to an embodiment of the invention, the alcohol can be
selected from saturation unitary, binary, One or more in more polynary
aliphatic alcohol and polyethylene glycol, poly- propyl alcohol etc..In
addition, it is optional, when When the alcohol is aliphatic alcohol,
one or more hydrogen on its alkyl chain part can also be by other
substituent institutes Substitution, the substituent can be, for
example, methyl, hydroxymethyl, cyclohexyl etc..
Preferably,
the alcohol can be one kind or more in cyclohexanol, nonyl alcohol,
polyethylene glycol and glycerine Kind.By using alcohol enumerated
above, formaldehyde can be quickly dissolved and absorbed.
Preferably,
the alcohol can be the polyethylene glycol that weight average
molecular weight is 200 to 400.In addition, formaldehyde Maximum level
in the polyethylene glycol that the weight average molecular weight is
200 to 400 is 50wt%, herein, The maximum level refers to the concept of
the amount for the whole formaldehyde that can enter in the
polyethylene glycol phase, i.e., at this With the amount of whole
formaldehyde existing for hemiacetal state and free state in
polyethylene glycol.
Wherein,
in step (2), the mol ratio that the alcohol prepares the formaldehyde
in product with step (1) is 0.1-3:1, preferably 0.5-1.5:1, more
preferably 1:1.
Wherein,
the temperature conditionss when gas-phase product is absorbed by
alcohol are 10-100 DEG C, preferably 30-80 DEG C, More preferably 60
DEG C.At this temperature, alcohol can effectively dissolve the
formaldehyde in the gas-phase product and be formed therewith
Hemiacetal.
In
the present invention, the reactor for implementing the step (2) does
not limit particularly, as long as it is can Realize the reactor of the
abundant exchange of gas-liquid, the example may include, but be not
limited to, spray column etc. all Plate column and packed tower etc..
According
to an embodiment of the invention, the pressure of the vacuum
distillation between the step (2) and (3) Power condition is
100-10mmHg, preferably 40-10mmHg, more preferably 20mmHg, and the
decompression The temperature conditionss of distillation are 40 to 80
DEG C, preferably 50-70 DEG C, more preferably 68 DEG C.In this
temperature and pressure Under the conditions of, water that can to
greatest extent in removing step (2) in the absorbent of gained, it is
ensured that the present invention is most The water content of
anhydrous formaldehyde made from end minimizes, simultaneously because
the decomposition bar for the hemiacetal that the present invention is
formed Part is more than 125 DEG C, therefore will not also cause the
decomposition of hemiacetal in alcohol, avoids the loss of formaldehyde.
In
the present invention, the reactor for implementing the vacuum
distillation does not limit particularly, as long as it is can be real
The reactor being now evaporated under reduced pressure, the example
may include, but be not limited to, thin film evaporation tower etc.
all be applicable Plate column and packed tower.It by the vacuum
distillation process according to the present invention, can contain
the dehydrate of generation Water reaches 0.001-0.01wt%, preferably
0.001wt%.
According
to an embodiment of the invention, the temperature conditionss of the
process of step (3) are preferably 130-170 DEG C, More preferably
140-160 DEG C;And pressure condition is normal pressure to 0.5MPa,
preferably normal pressure to 0.4MPa, More preferably normal pressure
is to 0.2MPa.Under the conditions of this temperature and pressure, no
water beetle can be obtained with stability and high efficiency
Aldehyde.
In
the present invention, the reactor of implementation steps (3) does not
limit particularly, as long as it is achievable The reactor of
temperature control heating, the example may include, but be not
limited to, the tower knot such as plate column and packed tower
Structure, while reactor can also be used.
In
the yield of the formaldehyde of preparation in accordance with the
present invention, i.e. step (3) amount of the formaldehyde of release
with It is more than 92% that formaldehyde of the present invention,
which prepares the ratio between amount of whole formaldehyde in the
gas-phase product reacted,.
[beneficial effect]
Embodiment 1
The
preparation that formaldehyde is carried out using methanol oxidizing
process is reacted, and the gas that content of formaldehyde is 30%
afterwards is from methanol Column overhead discharge is aoxidized,
temperature is down to after 60 DEG C, enters spray tower bottom with
330kg/h flow, together When polyethylene glycol (weight average
molecular weight 300) with 1000kg/h flows from spray column top spray,
so as to It is 16wt% to content of formaldehyde, content water is
5.4wt% formaldehyde absorption thing.The absorbent is through pump
afterwards Squeeze into thin film evaporation tower, be dehydrated,
contained under conditions of 68 DEG C of temperature, vacuum 25mm
mercury column Water is 0.005wt% dehydrate.The dehydrate is passed
through pyrolysis tower with 1100kg/h speed, 155 DEG C are pyrolyzed
with heating under normal pressure, so as to obtain the formaldehyde
gas that water content is 0.3wt%, yield 96%.
Calculation
formula:The amount for the formaldehyde that formaldehyde
yield=pyrolysis obtains/formaldehyde is prepared in the gas-phase
product of reaction The amount * 100% of formaldehyde
Publication number
Priority date
Publication date
Assignee
Title
US3423368A
*
1965-10-14
1969-01-21
Hary E Cier
Extractive recovery of formaldehyde
CN103339094A
*
2011-01-26
2013-10-02
宝理塑料株式会社
Method for producing hemiformal concentrate and method for producing formaldehyde gas
CN104710292A
*
2015-03-24
2015-06-17
江苏凯茂石化科技有限公司
Method for refining anhydrous pure formaldehyde gas and process device
Publication number
Priority date
Publication date
Assignee
Title
CN111440057A
*
2020-05-27
2020-07-24
无锡赫利邦化工科技有限公司
Preparation method for producing anhydrous formaldehyde by extractive distillation
CN111943822A
*
2020-09-22
2020-11-17
凯瑞环保科技股份有限公司
Device and method for producing high-concentration formaldehyde by using methanol
CN112521255A
*
2019-09-19
2021-03-19
山东辰信新能源有限公司
Preparation method of polyoxymethylene dimethyl ether and mixture thereof
WO2021052328A1
*
2019-09-19
2021-03-25
山东辰信新能源有限公司
Preparation method for polyoxymethylene dimethyl ether and mixture thereof
CN112574013A
*
2019-09-27
2021-03-30
山东辰信新能源有限公司
Preparation method of polymethoxy dimethyl ether (DMMn)
CN112898134A
*
2021-04-05
2021-06-04
山东辰信新能源有限公司
Dehydration and catalytic synthesis method and device for polymethoxy dimethyl ether
CN114057543A
*
2020-07-29
2022-02-18
山东辰信新能源有限公司
Recovery method of ineffective carrier in DMMn synthesis process
* Cited by examiner, † Cited by third party, ‡ Family to family citation
Publication
Publication Date
Title
CN107353188A
2017-11-17
A kind of method for preparing anhydrous gaseous formaldehyde
CN105566077B
2017-05-24
Process method for preparing polyoxymethylene dimethyl ethers
CN105669398B
2018-08-28
Produce the device and method of benzaldehyde
CN105503567B
2017-12-29
The device and method of continuous production benzoic acid, by-product benzaldehyde
CN103992206B
2016-09-07
Method and system for preparing isopentenol through ester exchange
CN106800500A
2017-06-06
A kind of process for preparing polymethoxy dimethyl ether
CN104193605A
2014-12-10
Environment-friendly formaldehyde preparation process
CN107445809B
2023-05-12
Device and method for producing concentrated formaldehyde
CN107602358A
2018-01-19
Method for preparing methoxy acetone by using micro-reaction device
CN105906492A
2016-08-31
Method for preparing hemiacetal methanol solution from methanol
CN107987037B
2021-07-16
Method for preparing epoxypropane in unit mode
CN101676252A
2010-03-24
Method for preparing acetal by using glyoxal
CN108218678A
2018-06-29
The separation and refining method and device of polymethoxy dimethyl ether
CN102649545B
2014-04-30
Nitric acid pre-concentration method for waste acid concentration technology in production of dinitrotoluene
CN104447254A
2015-03-25
Method for preparing 3-methoxy-4-hydroxybenzaldehyde
CN104513144A
2015-04-15
Method of recycling methanol in formaldehyde production through silver method
CN103214439B
2016-03-02
A kind of method of separating-purifying furfural
CN115253337B
2024-07-26
Method,
device and application for preparing isopropanol by two-tower thermal
coupling reaction-pressure swing mixed rectification
CN100352796C
2007-12-05
Process
of preparing benzaldehyde through continuous hydrolysis of ammonia
spirit catalytic of cinnamaldehyde in near critical water
2023-11-07
Method for synthesizing (+/-) -naproxen by using continuous flow micro-channel reactor oxidation
CN104402701A
2015-03-11
New process for synthetizing strawberry acid
CN219272982U
2023-06-30
Combined device for continuously preparing industrial glyoxylic acid
CN103877838B
2017-08-15
A kind of method for improving the nitric acid rate of recovery in Glucurolactone production
CN106268247A
2017-01-04
A kind of catalytic absorption method of formaldehyde
HCHO by methanol deshydro without Oxygen
CH3OH --->HCHO + H2
***********************************************************************************************************************
CN CN105170145A 王峰 中国科学院大连化学物理研究所
Priority 2014-06-20 • Filed 2014-06-20 • Published 2015-12-23
The
invention provides a catalyst for preparing anhydrous formaldehyde
through anoxic dehydrogenation of methanol. The catalyst is a metal
oxide supported precious metal nanoparticle. When the catalyst is
applied in a reaction for preparing anhydrous formaldehyde through
direct dehydrogenation of … Abstract
The
invention provides a catalyst for preparing anhydrous formaldehyde
through anoxic dehydrogenation of methanol. The catalyst is a metal
oxide supported precious metal nanoparticle. When the catalyst is
applied in a reaction for preparing anhydrous formaldehyde through
direct dehydrogenation of methanol, the reaction is carried out at a
low temperature, anhydrous formaldehyde is obtained in a high
selectivity manner, and the catalyst has high catalytic activity and
long service life.
Background technology
Formaldehyde is
a kind of important organic basic industrial chemicals, and in
macromolecular material, fine chemistry industry, organic synthesis,
medicine intermediate synthesis, fine perfumery synthesis, dyestuff
etc., have special applications, economic benefit is very
remarkable.Along with the rise of the engineering plastics of
synthesized high-performance, PARA FORMALDEHYDE PRILLS(91,95) demand is
increasing, and PARA FORMALDEHYDE PRILLS(91,95) concentration
requirement is day by day harsh.The existence of water have impact on
the exploitation of formaldehyde downstream product.When Lauxite, the
phenolic resins of synthesized high-performance, concentration of
formaldehyde directly has influence on rate of polymerization and the
degree of polymerization, affects the performance of product.And
industrial formaldehyde is mainly produced by methanol air oxidizing
process, formaldehyde water content is up to more than 50%.The
production of anhydrous formaldehyde generally adopts rare aldehyde
concentration technology and solvent azeotropic dehydration
concentration technology, and because the vapour pressure of formalin
is very low, easily form azeotropic system, dehydration separating
effect is not good, and energy consumption is large, and isolation
andpurification anhydrous formaldehyde is very difficult and
expensive.On the other hand, in methanol air oxidizing process, the
oxidizable formic acid of formaldehyde, etching apparatus.Therefore, in
the urgent need to studying new process, directly produce anhydrous
formaldehyde to meet the needs in market by methyl alcohol.
Methyl
alcohol direct dehydrogenation is a kind of effective ways preparing
anhydrous formaldehyde.The series of problems such as the stability of
formalin and purification are all easy to solve.At present, more
catalyst mainly a series of metal oxide, slaine, molecular sieve and
metal is studied.The research of metal oxide catalyst mainly
concentrates on CuO/SiO 2and ZnO/SiO 2.Result of study shows, these
catalyst all have good activity and selectivity, wherein ZnO/SiO
2catalyst activity is higher, but stability is generally poor.Weisgickl
etc. are with Na 0.5li 0.5alO 2for catalyst, can obtain 98% methanol
conversion and 75% formaldehyde selective, but its reaction temperature
will up to 900 DEG C, and require harsher to reactor, energy
consumption is high, uneconomical.Matsumura etc. are with the ZSM-5
molecular sieve of dealuminzation for catalyst, and formaldehyde yield
is 22%.Fudan University Dai Weilin and Fan Kangnian etc. have studied
loaded Ag catalyst, has good effect in methanol
dehydrogenation.Research finds Ag +be activated centre, in course of
reaction, be easily reduced into metallic state and inactivation.At
present, report methyl alcohol anaerobic dehydrogenation reaction
generally carry out under the high temperature conditions, under hot
conditions, formaldehyde is selective low, there is the problems such
as carbon distribution.Meanwhile, under high temperature and reducing
atmosphere, catalyst is easily reduced fast deactivation.Therefore, be
badly in need of exploitation and prepare novel low temperature
catalyst, suppressing side reaction generation and catalysqt
deactivation.
Summary of the invention
The object of this
invention is to provide the catalyst that a kind of methyl alcohol
anaerobic dehydrogenation prepares anhydrous formaldehyde, under
catalyst action, under anaerobic, cryogenic conditions, methyl alcohol
direct dehydrogenation, high selectivity obtains anhydrous formaldehyde.
Conventional
methanol anaerobic dehydrogenation process, adopts higher reaction
temperature, and high temperature easily makes side reaction occur, and
reduces the selective of formaldehyde.The present invention adopts the
noble metal nano particles catalyst of support type, realizes the
methanol dehydrogenation under cryogenic conditions, reduces the
generation of side reaction.The active component of catalyst is one or
more in Au, Pd, Pt, Ru metal, and the carrier of catalyst is MgO, CeO
2, ZrO 2, TiO 2, Al 2o 3, one or more in CaO.The load capacity of noble
metal is 0.2-15wt%, preferred 0.5%-5.0%.Noble metal nano particles
particle diameter is 1-5nm.
The preparation process of catalyst with
metal nanoparticles loaded is as follows: the metal component
soluble-salt aqueous solution of the 1wt% of certain mass and the
protective agent PVPK10 of certain mass are dissolved in 40mL deionized
water; then, 0.4wt% sodium borohydride or the reduction under PVPK10
protection of the potassium borohydride aqueous solution of certain
volume is added under agitation.This solution, in 20mL ethanol, joins
in above-mentioned solution by 0.2g support dispersion, stirs 12h,
solvent evaporate to dryness, washing 3-5 time, 80 DEG C of dry
12h.Obtained catalyst screening 20-40 order.
Reaction adopts fixed
bed quartz tube reactor on-line measuring device, inserts in quartz
reactor, use argon gas purge by obtained catalyst, and the air that
removing inside retains and impurity, carry out preheating under argon
shield; Wherein methyl alcohol volume content is 10%-60%; Reaction
temperature is 100-400 DEG C; The mass space velocity of bed is 5-85mLg
-1 cats -1; Particular methanol volume content is 35%-55%; Reaction
temperature is 200-300 DEG C; The mass space velocity of bed is
20-55mLg -1 cats -1.
Catalyst tool provided by the invention has the
following advantages: the catalytic activity of catalyst is high, (is
less than 400 DEG C) at relatively low temperature and reaches high
conversion ratio and selective.
Detailed description of the invention
Embodiment 1
Weigh
0.83g1wt%HAuCl 43H 2the O aqueous solution and 0.1gPVPK10 are dissolved
in 40mL deionized water, then, add 5mL0.4wt%NaBH under agitation 4.20mL
is dispersed with 0.2g carrier TiO subsequently 2ethanolic solution
join in above-mentioned solution, stir 12h under room temperature
condition, solvent evaporate to dryness, wash 3-5 time, 80 DEG C of dry
12h.Catalyst called after: 2wt%-Au/TiO 2(by Au, load capacity is 2wt%),
the average-size of Au ion is 2.5nm, and catalyst is numbered 1, and
have Electronic Speculum figure to find out, Au nano particle is
dispersed on carrier, and particle diameter is about 2nm.
E
Publication number
Priority date
Publication date
Assignee
Title
CN1970143A
*
2006-09-06
2007-05-30
大连理工大学
Method for preparing high-activity hydrogenation catalyst nano Ru/C
CN102553579A
*
2011-05-27
2012-07-11
中国科学院福建物质结构研究所
Preparation method of high-dispersity supported nano metal catalyst
CN103508863A
*
2012-06-29
2014-01-15
中国科学院大连化学物理研究所
Method for preparing anhydrous formaldehyde
JP2014030821A
*
2012-07-10
2014-02-20
Japan Organo Co Ltd
Platinum group metal supported contact dehydrogenation catalyst and contact dehydrogenation method
Publication number
Priority date
Publication date
Assignee
Title
CN105964245A
*
2016-05-05
2016-09-28
华东理工大学
Palladium catalyst and its preparation method and use
CN106423040A
*
2016-09-27
2017-02-22
厦门大学
Preparation method of precious metal microcell-embedded oxide composite material
CN107935832A
*
2017-12-30
2018-04-20
郑州智谷工业技术有限公司
A kind of method using fabricated by dehydrogenating alcohol for aldehyde or hemiacetal
CN109046350A
*
2018-08-03
2018-12-21
张家瑞
A kind of vehicle exhaust efficient process catalyst and preparation method thereof
CN109954493A
*
2017-12-14
2019-07-02
中国科学院大连化学物理研究所
The
rare-earth oxide supported ruthenium catalyst of preparing hydrogen by
ammonia decomposition and preparation and application
CN111217683A
*
2018-11-27
2020-06-02
中国科学院大连化学物理研究所
Method for preparing anhydrous formaldehyde by methanol dehydrogenation
CN111215062A
*
2018-11-27
2020-06-02
中国科学院大连化学物理研究所
Method for preparing anhydrous formaldehyde
Publication
Publication Date
Title
CN105170145A
2015-12-23
Catalyst for anoxic dehydrogenation of methanol, and application thereof
CN104028293B
2016-08-03
A kind of preparation method of cryogenic nitrogen doped graphene load nano Pd particle hydrogenation catalyst
CN101138730B
2010-08-11
Catalyzer for oxalic ester hydrogenation for synthesizing glycolate and method of preparing the same
CN102527377B
2013-12-04
High-efficiency
nano Pd catalyst used in the process of preparing oxalate through CO
carbonylation and prepared by dipping-controllable reduction method
CN104945262B
2016-09-14
A kind of method of catalysis methanol reduction dust technology methyl nitrite
CN104084217B
2017-03-08
Catalyst that a kind of ammonia nitrogen waste water CWO is processed and preparation method thereof
CN101767016B
2012-05-09
Aromatic aldehyde selective hydrogenation catalyst for refining terephthalic acid
Li et al.
2013
Selective Gas-Phase Oxidation of Alcohols over Nanoporous Silver.
CN103694116A
2014-04-02
Method for synthesizing methyl formate by gas-phase carbonylation of methyl alcohol
CN103657643A
2014-03-26
Method for preparing nano palladium metal catalyst
CN106866349A
2017-06-20
A kind of method of low temperature preparing chloroethylene by acetylene hydrochlorination
CN104001503B
2016-03-09
A kind of preparation method of graphene oxide-loaded nano Pd hydrogenation catalyst
CN107159217A
2017-09-15
A kind of Cu ZnO/SiO2Aeroge bimetallic catalyst and its production and use
CN106542972A
2017-03-29
A kind of method of normal temperature and pressure reducing carbonyl for methylene
CN105771974A
2016-07-20
Catalyst for producing hydrogen by catalyzing decomposition of formate at room temperature
CN103638947B
2015-08-26
A kind of Ni/Ag/Cu/TiO 2the preparation of composite catalyst and application thereof
CN102294240B
2013-02-13
Pd/C
catalyst for producing 2,3,5-trimethylhydroquinone (TMHQ) by virtue of
hydrogenation of 2,3,5-trimethylbenzoquinone (TMBQ) and preparation
method thereof
CN103638962B
2015-11-18
A kind of preparation of Ni/Cu/SBA-15 composite catalyst and application thereof
CN110327947A
2019-10-15
A kind of catalyst and the preparation method and application thereof of continuous production to methoxycyclohexyl ketone
CN106810419A
2017-06-09
For
graphene-supported metal composite in acetic acid preparation of ethanol
through hydrogenation catalyst and preparation method thereof
CN105622347B
2018-06-19
A kind of method that xylose prepares 1,2- pentanediols
CN104478664A
2015-04-01
Multiphase selective hydrogenation reaction method for cinnamyl aldehyde
CN106807366B
2020-02-07
Core-shell catalyst for preparing lactic acid and pyruvic acid from glycerol, and preparation and application thereof
Gao et al.
2016
Supported single Au (III) ion catalysts for high performance in the reactions of 1, 3-dicarbonyls with alcohols
CN103623861B
2015-08-26
A kind of preparation of Ni/Ag/MCM-41 composite catalyst and application thereof
*****************************************
CN111217683A
*
2018-11-27
2020-06-02
中国科学院大连化学物理研究所
Method for preparing anhydrous formaldehyde by methanol dehydrogenation
Abstract
The
invention relates to a method for preparing anhydrous formaldehyde by
methanol dehydrogenation. The method adopts a palladium-indium catalyst
(PdIn/SiO) supported by silicon dioxide2) The specific process is as
follows: PdIn/SiO2Filling the formed catalyst into a reaction tube,
then filling the reaction tube into a fixed bed reactor, injecting
methanol by an advection pump under normal pressure, taking inert gas
as carrier gas, wherein the methanol feeding ratio is 10-60 vol%, and
the methanol feeding speed is 0.10-0.30 mL/(g)cat.Min), reacting at
350-600 ℃, and obtaining the conversion rate of the methanol of 60-80%
and the selectivity of the formaldehyde of 65-85% by chromatography.
The invention relates to a method for preparing anhydrous formaldehyde
by methanol dehydrogenation, which adopts PdIn/SiO2As the catalyst, the
catalyst has higher catalytic activity and product selectivity, less
by-products, simple preparation process and high thermal stability.
Background
Formaldehyde
is an important organic chemical raw material, can be used for
producing thermosetting resins such as phenolic resin and melamine
resin, and bulk chemicals such as polyformaldehyde, phenolic aldehyde,
urotropine and 1, 4-butanediol, and is also a raw material for
synthesizing products such as dye, pesticide, disinfectant and adhesive.
At
present, the methanol oxidation method is generally adopted
industrially to prepare formaldehyde, theoretically, a formaldehyde
aqueous solution with the molar ratio of 1:1 is obtained, the vapor
pressure of the formaldehyde aqueous solution is low, the formaldehyde
and water form an azeotrope, the separation and purification of the
formaldehyde are very difficult, and the energy consumption is huge. In
recent years, the demand of engineering plastics, urotropine and other
medicines with excellent synthesis performance on anhydrous
formaldehyde is increasing, and the anhydrous formaldehyde is obtained
by removing moisture from industrial formaldehyde aqueous solution at
present, so that the direct preparation of the anhydrous formaldehyde
is a hot point of research.
The process for preparing formaldehyde
by anaerobic dehydrogenation of methanol obtains formaldehyde and
byproduct hydrogen, the formaldehyde and the byproduct hydrogen are
easy to separate, and the hydrogen is industrial gas with high added
value; the process has no water generation, avoids the separation
operation of the formaldehyde aqueous solution, and greatly saves the
purchase cost and the operation cost of the rectification equipment;
the process also avoids the problem that the formic acid generated by
the methanol oxidation method corrodes equipment. Therefore, the direct
dehydrogenation of methanol to prepare formaldehyde is a process with
great industrial prospect.
In recent years, a new anhydrous
formaldehyde preparation process with remarkable economic benefit draws
high attention at home and abroad, and a great deal of research work is
brought forward. Research efforts are currently focused on the
development of highly efficient catalysts, including metals and their
oxides, alkali metal salts, and molecular sieves, among others.
CN102274722A discloses a new type V2O3And a load type V2O3The
preparation method shows better activity in the dehydrogenation
reaction of methanol. Takagi et al (Takagi K, Morikawa Y, Ikawa
T.Chemestryletters, 1985, 14: 527-0Has high selectivity to
formaldehyde. CN101961650A discloses a homogeneous coprecipitation
method for preparing zirconium-based catalyst and catalyzing methanol
to perform anaerobic dehydrogenation, wherein the yield of formaldehyde
reaches 60%. Davirin et al (CN1390639A, CN1537673A, CN1544147A)
disclose a series of preparation methods of silver-based catalysts for
direct dehydrogenation of methanol. The patent CN101147872A takes
industrial sodium bicarbonate as a raw material to prepare the
anhydrous formaldehyde by catalyzing and preparing the industrial
sodium carbonate, and lays a foundation for the industrialization of
preparing the formaldehyde by methanol dehydrogenation. Music et al
(Music A, Batista J, Levec J. appliedCatalysis A: general, 1997, 165:
115-131) takes a ZSM-5 molecular sieve catalyst as a matrix, and
prepares Na-ZSM-5 and Cu-ZSM-5 type molecular sieves by an ion exchange
method, thereby obtaining better selectivity in the methanol
dehydrogenation reaction. CN105601487A discloses a rare earth complex
Ln [ CH ]2(CH2)nR]3·xH2O.yL, the catalyst has higher selectivity to
formaldehyde.
Based on the above, the disadvantages of the catalysts
currently used for the preparation of anhydrous formaldehyde are:
copper particles in the copper-based catalyst are distributed unevenly,
are larger, have smaller active surface area and lower activity; the
modified molecular sieve catalyst is difficult to regulate and control
in acid-base property and has more byproducts; the catalytic activity
of conventional carbonates or bicarbonates is relatively inert and the
reaction temperature is generally above 700 ℃. The complex catalyst is
a homogeneous catalysis process, and the separation energy consumption
is large. Therefore, a heterogeneous catalytic system with good
stability, high activity and formaldehyde selectivity and mild reaction
conditions is developed, and the preparation of anhydrous formaldehyde
by methanol dehydrogenation is imperative.
Disclosure of Invention
The
invention aims to overcome the defects of the catalyst used for
preparing anhydrous formaldehyde at present, such as: the acidity and
the alkalinity of the catalyst are difficult to control, and a
plurality of byproducts are generated. The patent combines a
palladium-indium alloy with higher activity and a nano-silica carrier
without a significant acid center to prepare a silica-supported
palladium-indium catalyst. The catalyst has the advantages of simple
preparation method, high stability, mild reaction conditions and high
conversion rate and selectivity.
The invention relates to a
preparation scheme of anhydrous formaldehyde, wherein the preparation
of the anhydrous formaldehyde adopts PdIn/SiO2As a catalyst, the
catalyst was molded and charged into a reaction tube, and then charged
into a fixed bed reactor. Under normal pressure, methanol is injected
by an advection pump, inert gas is used as carrier gas, the methanol
feeding ratio is 10-60 vol%, and the methanol feeding speed is
0.10-0.30 mL/(g)catMin), reacting at 350-600 ℃, and detecting a product
on line by gas chromatography.
The PdIn/SiO2A catalyst, wherein the
content of palladium is 0.5-5 wt% (by mass), and the content of indium
is 0.5-5 wt%. The PdIn/SiO2The catalyst is prepared by a
coprecipitation method and an impregnation method.
The PdIn/SiO2In
the preparation of the catalyst, the soluble precursor salt of
palladium is one or two of palladium nitrate, palladium ammonium
nitrate and sodium chloropalladate, and the soluble precursor salt of
indium is one or two of indium nitrate and indium chloride. The
PdIn/SiO2In the preparation of the catalyst, the soluble precursor salt
of palladium is preferably one or two of palladium ammonium nitrate and
sodium chloropalladate, and the soluble precursor salt of indium is
preferably indium chloride. The filling PdIn/SiO2The thickness of the
catalyst bed layer is 5-40 mm, the methanol feeding ratio is 10-60 vol%
(volume), and the methanol feeding speed is 0.10-0.30 ml/(g)catMin),
the reaction temperature is 350-500 ℃. The inert gas is one or more of
nitrogen, argon and helium.
This patent discloses silica supported
palladium indium catalysts with higher catalytic activity. The active
component palladium can activate C-H bonds of methanol and O-H bonds of
the methanol, and the introduction of indium effectively adjusts the
electronic structure and spatial distribution of the palladium,
inhibits the excessive dehydrogenation of the target product
formaldehyde at palladium sites, and obviously improves the selectivity
of the formaldehyde. And the palladium-indium has no obvious acid site,
so that the side reaction of dimethyl ether and water generated by
methanol dehydration catalyzed by acid is avoided while methanol
dehydrogenation is catalyzed, and the high-purity anhydrous
formaldehyde is favorably obtained. In addition, the catalyst related
to the patent adopts nano silicon oxide as a carrier, has large surface
area, is beneficial to high dispersion of palladium and indium, is not
easy to agglomerate and deactivate, and has no obvious acid center,
thereby avoiding side reaction caused by the acid center and further
improving the selectivity and stability of preparing anhydrous
formaldehyde by methanol dehydrogenation.
The specific implementation mode is as follows:
in
order to further explain the present invention in detail, several
specific embodiments are given below, but the present invention is not
limited to these embodiments.
Example 1
Coprecipitation method
for preparing (0.5 wt% Pd-0.5 wt% In)/SiO2Catalyst, operating as
follows: weighing 2g of nano SiO2(50nm), dispersing in 20mL of water,
adding one eachQuantitative Na2PdCl4And InCl3·4H2O, stirring for 1h,
and adjusting the pH value of the suspension to 11 by using 30% ammonia
water. Stirring for 1H, centrifuging, washing to neutrality, oven
drying at 80 deg.C, and drying at 500 deg.C H2Reducing for 2h to obtain
(0.5 wt% Pd-0.5 wt% In)/SiO2A catalyst. 2g of the catalyst was weighed,
tabletted, molded and packed into a fixed bed reactor. Under normal
pressure, nitrogen gas is used as carrier gas, methanol is injected by
an advection pump, the volume ratio of the methanol is 10 vol%, the
feeding speed of the methanol is 0.30mL/(gcat. min), the reaction is
carried out at 350 ℃, the conversion rate of the methanol is 73% by gas
chromatography online detection, and the selectivity of the
formaldehyde is 66%.
Publication number
Priority date
Publication date
Assignee
Title
EP0130068A2
*
1983-06-23
1985-01-02
Sumitomo Chemical Company, Limited
A process for producing formaldehyde
US5103066A
*
1990-12-10
1992-04-07
Mobil Oil Corp.
Dehydrogenation of alcohols over non-acidic metal-zeolite catalysts
WO2008006792A1
*
2006-07-11
2008-01-17
Basf Se
A method for dehydrating alcohols
CN105170145A
*
2014-06-20
2015-12-23
中国科学院大连化学物理研究所
Catalyst for anoxic dehydrogenation of methanol, and application thereof
Publication
Publication Date
Title
CN102227401B
2014-06-18
Carbonylation process for production of methyl acetate
CN106140156A
2016-11-23
A kind of activated carbon supported rhodium base catalyst and its preparation method and application
CN103508863B
2016-04-27
A kind of method preparing anhydrous formaldehyde
CN109999896B
2020-09-25
High-efficiency
catalyst applied to preparation of cyclohexanone by selective
hydrogenation of phenol and preparation method thereof
CN105732349A
2016-07-06
Method for preparing anhydrous formaldehyde through methanol dehydrogenation
CN105732350A
2016-07-06
Method of producing anhydrous formaldehyde through oxygen-free dehydrogenation
CN104447248A
2015-03-25
Preparation method for anhydrous formaldehyde
CN102580754A
2012-07-18
Catalyst for synthesizing methyl acetate as well as preparation method and application
CN111763145B
2021-11-16
Method for synthesizing acrylic acid from methyl acetate aqueous solution
CN107486191B
2020-06-23
Iridium-based catalyst loaded on acid-treated carbon carrier and preparation method and application thereof
CN101619048A
2010-01-06
Method for synthesizing propylene oxide
CN111217683A
2020-06-02
Method for preparing anhydrous formaldehyde by methanol dehydrogenation
CN102757310B
2015-04-29
Method of preparing isopropanol by catalytic conversion of cellulose
CN111763143A
2020-10-13
Method for synthesizing acrylic acid
CN111215062A
2020-06-02
Method for preparing anhydrous formaldehyde
CN109704917B
2023-09-15
Process for chemically converting corncob furfural residues into bioethanol
CN111217687A
2020-06-02
Method for preparing anhydrous formaldehyde
CN1024464C
1994-05-11
Method for preparing isoborneol by catalyzing camphene hydration with resin
CN110981698B
2022-04-19
Preparation method of 3-methyl-2-butenol
CN101502805B
2011-01-12
Catalyst for preparing acetic anhydride as well as preparation method and application
CN102249989B
2015-01-28
Method for preparing 3-methylpyridine by utilizing acrolein
CN102500420A
2012-06-20
Alcohol gas phase dehydrogenation catalyst, preparation method thereof and application
CN103480376B
2015-01-14
Preparation method and application of synthetic carboxylate copper-mesoporous zirconium bifunctional catalyst
US5103066A
*
1990-12-10
1992-04-07
Mobil Oil Corp.
Dehydrogenation of alcohols over non-acidic metal-zeolite catalysts
EXAMPLE 1
The
dehydrogenation of isopropanol to acetone was accomplished using a
non-acidic Pt/Sn-ZSM-5 as a catalyst. This catalyst contained 0.53% Pt,
1.23% Sn, 0.56% Na, and less than 0.01% Al. The catalyst was prepared in
accordance with the disclosure of allowed U.S. application Ser. No.
211,198, filed June 24, 1988 now U.S. Pat. No. 4,990,710 which is relied
upon and incorporated by reference herein; Example 3 below is
illustrative. The reaction was conducted at 300° C. and atmospheric
pressure, with a 5.2 IPA WHSV and a H
2
/IPA ratio of 1. Under these conditions, an 87% yield of acetone was
obtained. By-products constituted just over 3 weight %. No significant
aging was observed over a period of five days.
Publication number
Priority date
Publication date
Assignee
Title
US2861106A
*
1954-02-26
1958-11-18
Knapsack Ag
Process of preparing aldehydes or ketones by dehydrogenation of alcohols
GB823514A
*
1957-05-02
1959-11-11
Engelhard Ind Inc
Dehydrogenation of alcohols
US3013990A
*
1961-09-11
1961-12-19
Union Carbide Corp
Iron group metal catalyst
US3702293A
*
1971-12-30
1972-11-07
Universal Oil Prod Co
Hydrocarbon conversion process with a bimetallic catalyst
US3702294A
*
1971-05-10
1972-11-07
Universal Oil Prod Co
Trimetallic hydrocarbon conversion catalyst and uses thereof
US3778477A
*
1971-04-21
1973-12-11
Basf Ag
Manufacture of alpha,beta-unsaturated carbonyl compounds
US3878131A
*
1971-09-29
1975-04-15
Universal Oil Prod Co
Multicomponent dehydrogenation catalyst
US3981923A
*
1969-06-11
1976-09-21
Shell Oil Company
Dehydrogenation of alcohols to ketones
US4104320A
*
1975-09-10
1978-08-01
Elf-Union
Method of dehydrocyclizing aliphatic hydrocarbons
USRE29948E
*
1973-11-02
1979-03-27
Mobil Oil Corporation
Crystalline silicates and catalytic conversion of organic compounds therewith
GB2033358A
*
1978-11-06
1980-05-21
Mobil Oil Corp
Crystalline Zeolite Compositions
US4325808A
*
1980-07-21
1982-04-20
Standard Oil Company (Indiana)
Hydrocarbon conversion catalyst system and method
US4347394A
*
1980-12-10
1982-08-31
Chevron Research Company
Benzene synthesis
EP0074651A1
*
1981-09-16
1983-03-23
Hoechst Aktiengesellschaft
Zeolites containing gallium and/or indium, process for producing them and their use
US4387258A
*
1981-01-28
1983-06-07
Exxon Research & Engineering Co.
Selective hydrogenation using palladium/platinum on crystalline silica polymorph/silicalite/high silica zeolite
FR2520636A1
*
1982-02-01
1983-08-05
Chevron Res
L-TYPE ZEOLITIC COMPOSITION CONTAINING PLATINUM AND BARIUM AND ITS APPLICATION TO HYDROCARBON REFORMING
US4416806A
*
1981-04-10
1983-11-22
Elf France
Catalyst for production of aromatic hydrocarbons and process for preparation
US4418006A
*
1980-07-21
1983-11-29
Standard Oil Company (Indiana)
Hydrocarbon conversion catalyst system
US4435283A
*
1982-02-01
1984-03-06
Chevron Research Company
Method of dehydrocyclizing alkanes
EP0107389A2
*
1982-09-28
1984-05-02
Exxon Research And Engineering Company
Improved zeolite L catalyst for reforming
US4456527A
*
1982-10-20
1984-06-26
Chevron Research Company
Hydrocarbon conversion process
US4486547A
*
1981-11-05
1984-12-04
Uop Inc.
Indium-containing dehydrogenation catalyst
US4487843A
*
1983-03-09
1984-12-11
British Petroleum Company, P.L.C.
Catalytic activity of aluminosilicate zeolites
US4487848A
*
1983-06-02
1984-12-11
Uop Inc.
Indium-containing catalyst for reforming hydrocarbons
US4547472A
*
1984-05-29
1985-10-15
Chevron Research Company
Method of adding an alkaline earth metal to a zeolitic catalyst
US4560804A
*
1982-09-21
1985-12-24
Exxon Research & Engineering Co.
Catalytic process for the manufacture of ketones
US4576805A
*
1982-08-27
1986-03-18
Mobil Oil Corporation
Increasing lattice metal content of porous inorganic crystalline compositions
US4588495A
*
1984-02-23
1986-05-13
Institut Francais Du Petrole
Catalytic reforming process
US4604371A
*
1981-06-19
1986-08-05
Union Oil Company Of California
Oxidation catalyst
US4614834A
*
1984-11-05
1986-09-30
Uop Inc.
Dehydrocyclization with nonacidic L zeolite
US4822942A
*
1987-12-28
1989-04-18
Mobil Oil Corporation
Styrene production
US4830729A
*
1987-12-28
1989-05-16
Mobil Oil Corporation
Dewaxing over crystalline indium silicates containing groups VIII means
US4849567A
*
1987-12-28
1989-07-18
Mobil Oil Corporation
Catalytic dehydrogenation of hydrocarbons over indium-containing crystalline microporous materials
US4851599A
*
1988-06-24
1989-07-25
Mobil Oil Corporation
Styrene production
US4868145A
*
1987-12-28
1989-09-19
Mobil Oil Corporation
Dehydrogenation and dehydrocyclization catalyst
US4882040A
*
1988-06-24
1989-11-21
Mobil Oil Corporation
Reforming process
US4886926A
*
1988-06-24
1989-12-12
Mobil Oil Corporation
Catalytic dehydrogenation of hydrocarbons over tin-containing crystalline microporous materials
US4892645A
*
1988-06-24
1990-01-09
Mobil Oil Corporation
Dewaxing catalyst based on tin containing materials
US4910357A
*
1988-06-24
1990-03-20
Mobil Oil Corporation
Alkylate upgrading
US4931416A
*
1988-06-24
1990-06-05
Mobil Oil Corporation
Thallium
or lead-containing microporous crystalline materials and their use as
dehydrogenation dehydrocyclization and reforming catalysts
US4935566A
*
1987-11-17
1990-06-19
Mobil Oil Corporation
Dehydrocyclization and reforming process
*************************************************************************
EP0130068A2
*
1983-06-23
1985-01-02
Sumitomo Chemical Company, Limited
A process for producing formaldehyde
Abstract
An improved process
for producing formaldehyde in a gas-phase reaction wherein the
dehydrogenation of methanol is conducted with a catalyst, which is zinc
oxide and/or indium oxide or a mixture of silica and one or more of
these oxide, to give formaldehyde in a high yield.
(2). Catalyst Reaction Test:- [0048]
In
a quartz tubular reaction, a mixture of 2.0 g of a sample catalyst and
2.0 g of 40 - 60 mesh fused alumina, which was previously proved to be
inert in the test reaction, was charged. Methanol was vaporized and
mixed with nitrogen at 150°C, and the gaseous mixture (molor ratio, CH30H/N2
= 36/65) was passed through at atmospheric presusre at 250 m mol/hr,
whereby the dehydrogenation of methanol was effected at 500° to 600°C.
However, in Examples 3 and 4, a gaseous mixture (molar ratio, CH30H/N2 = 42/58) was fed at 375.9 m mol/hr at atmospheric pressure. In Example 13, a gaseous mixture (molar ratio, CH3OH/N2
= 21/79) was fed at 439.5 m mol/hr at atmospheric pressure and, in
Example 14, the molar ratio of methanol to nitrogen was 17/83 and
feeding rate of the gaseous mixture was 553.1 m mol/hr at atmospheric
pressure. In Examples 13 and 14, no alumina was used and only the sample
catalyst was packed in the reactor.
- [0049]
The
gas exhausted from the reactor was directly introduced, with a sampler,
to a gas chromatography (heat electroconductivity type) in which a 3 m
column packed with APS-201 20 % Flusin (manufactured by Gasukuro Kogyo
Inc.) and a 2 m column packed with molecular sieve 13X are used, and the
concentrations of formaldehyde (HCHO), methyl formate, dimethyl ether
(DME),hydrogen (H2), carbon monoxide (CO), methane (CH4), unreacted methanol (CH30H
at the exit) and nitrogen were measured. The results are given in
Tables 1 and 2. The data of Examples 1 to 14 and Comparative Examples 1
to 8 were those measured at 8 to 12 hours after the reaction temperature
reached to the previously determined value and therefore of the steady
state. Since almost no dimethyl ether and methyl formate were detected
with the gas chromatographic analysis, the corresponding data are
omitted from the Table 1, but no data are given in Table 2, with respect
to
Publication number
Priority date
Publication date
Assignee
Title
CH202236A
*
1936-06-10
1939-01-15
Natta Giulio
Process for the production of a zinc oxide catalyst for the synthesis of methanol.
FR2397877A1
*
1977-07-22
1979-02-16
Moller Carl
CATALYST FOR DEHYDROGENATION OF ORGANIC COMPOUNDS ESPECIALLY OF AMINES, THIOLS AND ALCOHOLS AND A PREPARATION PROCESS
DE3006105A1
*
1979-02-19
1980-08-28
Johnson Matthey Co Ltd
INDIUM CATALYSTS
JPS52215A
*
1975-06-20
1977-01-05
Mitsubishi Gas Chem Co Inc
Process for preparation of formaldehyde
Publication number
Priority date
Publication date
Assignee
Title
EP0261867A2
*
1986-09-24
1988-03-30
Sumitomo Chemical Company, Limited
Process for producing formaldehyde
EP0294684A2
*
1987-06-06
1988-12-14
Hoechst Aktiengesellschaft
Method for the production of formaldehyde
CN105642286A
*
2016-03-02
2016-06-08
中国科学院山西煤炭化学研究所
Preparation method of nano copper oxide @ mesoporous silica core-shell structure material
CN111217683A
*
2018-11-27
2020-06-02
中国科学院大连化学物理研究所
Method for preparing anhydrous formaldehyde by methanol dehydrogenation
CN1103244C
*
1999-08-09
2003-03-19
中国石油化工集团公司
Novel load silver catalyst and preparation process thereof
US6563006B2
2001-04-30
2003-05-13
Melvin K. Carter
Catalytic oxidative conversion of hydrocarbons to aldehydes
CN105597756A
*
2016-03-02
2016-05-25
中国科学院山西煤炭化学研究所
Copper-based
core-shell catalyst for preparing methyl formate through methyl alcohol
dehydrogenation and preparation method and application thereof
CN111215062A
*
2018-11-27
2020-06-02
中国科学院大连化学物理研究所
Method for preparing anhydrous formaldehyde
********************************************************************************************************
JPS52215A
*
1975-06-20
1977-01-05
Mitsubishi Gas Chem Co Inc
Process for preparation of formaldehyde
also US4054609A
Abstract
PURPOSE:Formaldehyde,
having good thermal and aging stabilities, is prepared in high yield by
the dehydrogenation of methy alcohol in the presence of the catalyst
consisting of Cu, Zn and Se.
Description
The present
invention relates to a process for the preparation of formaldehyde by
dehydrogenation of methanol. More particularly, it relates to a process
for the preparation of formaldehyde by the dehydrogenation of methanol
in the presence of copper, zinc and selenium as catalyst components.
Catalytic
oxidative dehydrogenation, catalytic oxidation and the like are
generally known as a commercially available process for the preparation
of formaldehyde. According to these prior art processes, formaldehyde
is generally obtained as an aqueous solution whose concentration is
found to be at most 40% by weight.
These aqueous formaldehyde
solutions are very unstable, and so they are not satisfactory in both
quality and handling. For instance, precipitation of paraformaldehyde
during storage and transportation, as well as formation of formic acid
by a side reaction, may befrequently observed. Further,
paraformaldehyde which is obtained by the concentration of the aqueous
formaldehyde solution has a defect that its solubility decreases
several days after the preparation although the paraformaldehyde
obtained just after the preparation is comparatively well soluble in
water, an alcohol, etc. in a few days after the preparation.
On the
other hand, there have been proposed many methods for the production of
formaldehyde by the so-called dehydrogenation of methanol. For example,
a method using a catalyst consisting of copper, silver and silicon (see
U.S. Pat. No. 2,939,883), a method using a catalyst having metallic
zinc adhered on the surface of a metallic copper support (Japanese
Patent Publication No. 11,853/1966), a method using fused zinc,
gallium, indium or aluminum or an alloy thereof (Japanese Patent
Publication No. 19,251/1972), and a method contacting methanol with
fused zinc containing carbon or a zinc alloy containing carbon
(Japanese Patent Laid Open No. 97,808/1973) have been proposed.
However, even these methods have common serious disadvantages in that
the life of their catalysts and the conversion obtained are so poor as
to make these methods not industrially acceptable.
We also proposed
several processes for the preparation of formaldehyde in a high yield
by using a novel catalyst: a process wherein a catalyst prepared from
copper, zinc and sulfur is used (Japanese Patent Application No.
63,984/1974) and a process wherein sulfur is fed in gaseous state in
order to prevent deterioration of the catalyst (Japanese Patent
Application No. 148,390/1974). These processes are superior to the
prior art processes in that the catalysts have high activity; but the
sulfur undesirably entrains into the reaction product or the exit gas
in accordance with these process because of using sulfur as the
catalyst.
Accordingly, it is an object of the present invention to provide a novel process for the preparation of formaldehyde.
Another
object of the present invention is to provide a process for the
preparation of formaldehyde by dehydrogenation of methanol by using a
catalyst without any sulfur-exhausting problem.
A further object of
the present invention is to provide a process for the preparation of
formaldehyde which is excellent in both thermal stability and storage
stabilility. A still further object of the present invention is to
provide an excellent catalyst for the preparation of formaldehyde.
In
accordance with the present invention, these objects can be
accomplished by a process for the preparation of formaldehyde
comprising subjecting methanol to dehydrogenation in the presence of a
ternary metal catalyst comprising copper, zinc and selenium.
The
atomic ratio of these metals constituting the catalyst of the present
invention may be as follows: copper/zinc/selenium 1:0.01-0.5:0.01-0.5,
preferably 1:0.1-0.4:0.1-0.4, provided the amount of selenium
preferably should not exceed that of zinc.
The catalyst used in the
present invention may be prepared by any one of conventional procedures
known to those skilled in the art, for example, precipitation method,
thermal decomposition method, or deposition and drying method. Any of
these procedures may be properly selected based on the raw material to
be used.
The raw materials for the catalyst in the present invention
include a copper salt of a mineral acid such as copper nitrate, copper
chloride, copper sulfate and copper sulfite, etc., copper hydroxide,
copper oxide, basic copper cabonate, metallic copper, etc. as a copper
source; a zinc salt of a mineral acid such as zinc nitrate, zinc
chloride, zinc sulfate and zinc sulfite, etc., zinc hydroxide, zinc
oxide, metallic zinc as a zinc source; and selenic acid, selenious
acid, selenium oxide, metallic selenium, etc. as a selenium source.
Further, zinc selenide, zinc selenate, zinc selenite, etc. may be used
as both zinc and selenium sources and copper selenide may be used as
both copper and selenium sources.
The raw material for the catalyst may be in the form of either powder or grains, etc.
The
above raw materials may be formed to a particle having a desired shape
which may be tablet, sphere or the like and the average diameter of the
particles thus formed would be more than 1 mm, preferably 2 to 5 mm.
The catalyst particles are then reduced in a reductive atmosphere, for
example, in two steps, first at a temperature of 100° to 300° C,
preferably 150° to 250° C for more than 0.2 hour, preferably 0.5 to 1
hour and then at the temperature of 500°-750° C, preferably 600°-700° C
for more than 0.1 hour, preferably 0.5-1 hour.
The reaction
temperature for the present invention may be 500° to 750° C, preferably
600° to 700° C in a catalyst bed. If it is below 500° C, conversion
decreases, and if it is higher than 750° C, yield decreases. This
reaction temperature is a temperature conventionally employed in the
art.
The dehydrogenation reaction in the present invention,
generally, may be carried out under atmospheric pressure. However, it
may be carried out under reduced or superatmospheric pressure, if
desired.
Methanol is generally fed in vapor form together with
hydrogen gas to the catalyst bed. Methanol may be preferably fed in an
amount of 0.2 to 0.7 mol/hr per 20 ml of the catalyst. The feed amount
of less than 0.2 mol/hr is not practical, whereas that of more than 0.7
mol/hr shows decreased conversion of methanol.
According to the
present invention, the product obtained contains 30 to 85% by weight of
formaldehyde, 0 to 2% by weight of water and the balance of methanol.
It is to be appreciated that formaldehyde can be obtained in a high
yield, with a very small water content.
The product obtained in
accordance with the present invention has quite a different property
from an aqueous formaldehyde solution or paraformaldehyde prepared by
any conventional method. That is to say, when the formaldehyde
concentration in the product obtained by the present invention is not
more than 70% by weight, the product is a clear liquid at an ordinary
temperature and does not show any appreciable solid precipitation, even
if it is left alone at an ordinary temperature for a long period of
three months or more. When the formaldehyde concentration is more than
70% by weight, the product is a white solid at ambient temperature, but
it melts easily by heating to form a clear liquid, and then it becomes
solid again on cooling. Even if such melting by heating and
soldification by cooling are repeated, the fusion temperature does not
change. For example, the product in the present invention containing
73.0% by weight of formaldehyde, 25.9% by weight of methanol and 1.1%
by weight of water is solid at ordinary temperature, but it becomes a
clear liquid by heating at a temperature of 30° to 35° C and it
solidifies again by cooling. Such a heating-cooling cycle is repeated
once a day for 30 days, but the melting temperature did not change.
This fact shows that the product obtained by the present invention is
more stable compared with those obtained by the prior art processes.
The present invention is illustrated in detail by the following examples, in which conversion and yield are defined as follows:
EXAMPLE 1
Each
aliquot, 50.0 g of cupric oxide, 7.0 g of selenium dioxide and 7.0 g of
zinc oxide, was ground and mixed thoroughly in a kneader. Thereto, 30
ml of water was added to obtain a paste, which was in turn formed into
tablets each being 3 mm in diameter and 3 mm in height. The tablets
thus obtained were reduced in a hydrogen gas stream at a temperature of
200° C and then at a temperature of 650° C respectively for 30 minutes
to obtain a catalyst.
20 ml of the catalyst thus obtained was packed
in a quartz glass-made tubular reactor having an inner diameter of 21
mm, and 15.0 g (0.468 mol)/hr of methanol vapor and an equimolar amount
of hydrogen gas were fed thereto continuously from one end of the
reactor and subjected to reaction at a catalyst bed temperature of 650°
C. Conversion of 78.1% and yield of 66.0% were obtained. The catalytic
activity was maintained for more than 50 hours. Composition of the
product is 73.0% by weight of formaldehyde, 1.1% by weight of water and
25.9% by weight of methanol in the condensed phase and 87.3% by volume
of hydrogen, 9.1% by volume of carbon monoxide, 2.7% by volume of
methane and 0.9% by weight of carbon dioxide in the gas phase. The gas
phase constitutes 15% by weight on total weight basis while the
condensed phase comprises 85% by weight.
The amount and composition of the gas phase is nearly the same all in the following examples.
EXAMPLE 2
A
catalyst was prepared from 40.0 g of cupric oxide and 14.5 g of zinc
selenide as raw materials in the same manner as in EXAMPLE 1. The
reaction was carried out by using the catalyst under the same
conditions as in EXAMPLE 1 thereby to obtain a conversion of 73.8% and
a yield of 64.5%. The catalytic activity was maintained over more than
55 hours. Further, the composition of the product in the condensed
phase was 69.3% by weight of formaldehyde, 0.7% by weight of water and
30.0% by weight of methanol.
EXAMPLE 3
A catalyst was prepared
from 50.0 g of powdered copper and 60.6 g of zinc selenite as raw
materials in the same manner as in EXAMPLE 1. The reaction was carried
out under the same conditions as in EXAMPLE 1 to obtain a conversion of
69.0% and yield of 62.1%. The catalytic activity was maintained over
more than 50 hours. The composition of the product in the condensed
phase was 64.9% by weight of formaldehyde, 0.5% by weight of water and
34.6% by weight of methanol.
EXAMPLE 4
A catalyst was prepared
from 50.0 g of cupric hydroxide anhydride and 2.0 g of zinc selenide as
raw materials in the same manner as in EXAMPLE 1. The reaction was
carried out under the same conditions as in EXAMPLE 1 to obtain a
conversion of 65.5% and a yield of 59.4%. The catalytic activity was
maintained over more than 35 hours. Composition of the product in the
condensed phase was 61.5% by weight of formaldehyde 0.5% by weight of
water and 38.0% by weight of methanol.
EXAMPLE 5
Copper nitrate
trihydrate (242.0 g) and zinc nitrate hexahydrate (40.7 g) were
dissolved in 1500 ml of water to obtain nitrate solution. Separately,
sodium hydroxide (91.0 g) was dissolved in 500 ml of water to obtain an
aqueous sodium hydroxide solution and the aqueous solution was added
dropwise to the nitrate solution over 1 hour. The precipitate thus
obtained was separated by filtration and then dispersed into about 1500
ml of water. The resulting dispersion was vigorously stirred for 15
minutes and was filtered with stirring to obtain a cake. Such washing
procedure as above was repeated six times. Selenium dioxide (11.1 g)
was added to the cake thus obtained and the cake was crushed, mixed,
formed and reduced in the same manner as in EXAMPLE 1 to obtain a
catalyst.
The reaction was carried at a catalyst bed temperature of
680° C by using the catalyst thus obtained under the same conditions as
in EXAMPLE 1 to obtain a conversion of 88.5% and a yield of 57.6%. The
catalytic activity was maintained over more than 50 hours. The
composition of the product in the condensed phase was formaldehyde
(81.4% by weight), water (1.3% by weight) and methanol (17.3% by
weight).
COMPARATIVE EXAMPLE 1
A catalyst was prepared in the
same manner as in EXAMPLE 1 but without using selenium dioxide. The
reaction was carried out using the catalyst under the same conditions
as in EXAMPLE 1 to obtain a conversion of 98.2% and a yield of 12.2%.
The yield was considerably lower than those of the EXAMPLES.
COMPARATIVE EXAMPLE 2
A
catalyst was prepared in the same manner as in EXAMPLE 1 but without
using zinc oxide. The reaction was carried out by using the catalyst
under the same conditions as in EXAMPLE 1 to obtain a conversion of
about 60% and a yield of about 50%, after 1 to 2 hours from the start
of the reaction. The catalytic activity, however, deteriorated
gradually, and conversion and yield decreased respectively to 40% and
35% after 5 hours from the start.
EXAMPLE 6
EXAMPLE 1 was
repeated, except that the reaction was carried out at a catalyst bed
temperature of 700° C. in place of the catalyst bed temperature of 650°
C., thereby to obtain a conversion of 90.2% and a yield of 55.1%. The
catalytic activity was maintained over more than 50 hours. Further, the
composition of the product in the condensed phase was 83.6% by weight
of formaldehyde, 0.6% by weight of water and 15.8% by weight of
methanol.
EXAMPLE 7
EXAMPLE 1 was repeated, except that the
reaction was carried out at a catalyst bed temperature of 600° C. in
place of the catalyst bed temperature of 650° C., thereby to obtain a
conversion of 60.2% and a yield of 55.3%. The catalytic activity was
maintained over more than 70 hours. Further, the composition of the
product in the condensed phase was 55.5% by weight of formaldehyde,
1.9% by weight of water and 42.6% by weight of methanol.
EXAMPLE 8
A
catalyst was prepared from 50.0 g of cupric oxide, 5.0 g of zinc
hydroxide and 5.6 g of selenium dioxide as raw materials in the same
manner as in EXAMPLE 1. The reaction was carried out by using the
catalyst under the same conditions as in EXAMPLE 1 thereby to obtain a
conversion of 93.4% and a yield of 49.3%. The catalytic activity was
maintained over more than 50 hours. Further, the composition of the
product in the condensed phase was 87.2% by weight of formaldehyde,
0.4% by weight of water and 12.4% by weight of methanol.
EXAMPLE 9
A
catalyst was prepared from 50.0 g of cupric oxide, 15.0 g of zinc oxide
and 14.4 g of selenium powder as raw materials in the same manner as in
EXAMPLE 1. The reaction was carried out by using the catalyst under the
same conditions as in EXAMPLE 1 thereby to obtain a conversion of 53.7%
and a yield of 48.8%. The catalytic activity was maintained over more
than 60 hours. Further, the composition of the product in the condensed
ph
ase was 48.8% by weight of formaldehyde, 1.9% by weight of water and 49.3% by weight of methanol.
Claims (6)
Hide Dependent
What we claim is:
1.
A process for the preparation of formaldehyde, comprising subjecting
methanol in the vapor phase to dehydrogenation in the presence of a
catalytically effective amount of a catalyst consisting of copper, zinc
and selenium as catalyst components at a temperature of 500° to 750° C.
wherein the atomic ratio of said catalyst components is 1:0.1-0.5 :
0.01-0.5 for Cu:Zn:Se.
2. A process according to claim 1, wherein the dehydrogenation was carried out at a temperature of 600° to 700° C.
3. A process according to claim 1, wherein the catalyst has the copper/zinc/selenium atomic ratio of 1:0.1-0.4:0.1-0.4.
4. A process according to claim 1, wherein the methanol is fed together with hydrogen gas to a catalyst bed.
5.
A process according to claim 1, wherein the methanol is fed to a
catalyst bed in an amount of 0.2 to 0.7 mol/hr per 20 ml of the
catalyst.
6. A process according to claim 5, wherein the methanol is fed with hydrogen gas, to a catalyst bed.
Patent Citations (2)
Publication number
Priority date
Publication date
Assignee
Ti
DE3004436A1
*
1980-02-07
1981-08-13
Basf Ag, 6700 Ludwigshafen
METHOD FOR PRODUCING FORMALDEHYDE
DE3470031D1
*
1983-06-23
1988-04-28
Sumitomo Chemical Co
A process for producing formaldehyde
US4595396A
*
1984-05-14
1986-06-17
Phillips Petroleum Company
Composition comprising 1,3,5-trioxane
JPH078812B2
*
1986-09-24
1995-02-01
住友化学工業株式会社
Formaldehyde manufacturing method
US6160186A
*
1998-11-12
2000-12-12
Bp Amoco Corporation
Preparation
of polyoxymethylene dimethyl ethers by catalytic conversion of dimethyl
ether with formaldehyde formed by dehydrogenation of dimethyl ether
US6437195B2
*
1998-11-12
2002-08-20
Bp Corporation North America Inc.
Preparation
of polyoxymethylene dimethyl ethers by acid-activated catalytic
conversion of methanol with formaldehyde formed by dehydrogenation of
methanol
US7622421B2
*
2005-03-11
2009-11-24
Philip Morris Usa Inc.
Catalysts for low temperature oxidation of carbon monoxide
* Cited by examiner, † Cited by third party, ‡ Family to family citation
*****************************************************************************************************************
DE3004436A1
*
1980-02-07
1981-08-13
Basf Ag, 6700 Ludwigshafen
METHOD FOR PRODUCING FORMALDEHYDEThe invention relates to a process for the production of formaldehyde by the dehydrogenation of methanol in the presence
of copper, zinc: and tellurium-containing catalysts at a temperature of 300 to 750 ° C.
It
is known from the German Auslegeschrift 11 44 252 and from Ullmanns
Encyklopadie der technischen Chemie (4th edition), Volume 11, pages 693
to 696, methanol in the presence of metal oxide catalysts, usually 'on
iron oxide and molybdenum oxide without a carrier to formaldehyde to
oxidize. A corresponding catalyst, which also contains cobalt oxide,
describes the German patent specification 11 02 344. The German
Auslegeschrift 10 63 14 l teaches the oxidation in the presence of such
catalysts on a support, carbide and / or iron oxide supports being used.
Temperatures from 270 to 380 °
C. are specified. All of these processes yield 37 to 55 percent
strength by weight, aqueous formaldehyde solutions by means of catalytic
oxidation. The storage and transport of such solutions cause
difficulties, since paraformaldehyde precipitates and corresponding
deposits and blockages occur in the systems, unless stabilizers or
increased storage temperatures are used. Elevated storage temperatures
favor the formation of formic acid. This process does not produce
low-water methanolic formaldehyde.
For
these reasons, processes for the production of low-water formaldehyde
solutions with copper / silver / silicon have already been established
or copper / zinc or zinc / gallium / indium developed as catalysts,
aluminum catalysts and zinc catalysts,
those described in German Offenlegungsschrift 25 25 174
will. A dehydrogenation of methanol vapor in a mixture with hydrogen and
copper is more advantageous,
u J
1 30033/0344
BASF Aktiengesellschaft - / - OZ 0050/0 ^ 274
'Zinc and sulfur as catalyst components at 500 to 75O 0
C viewed. In the German Offenlegungsschrift 26 27 ^ 21, a similar
procedure, which uses selenium as a catalyst component instead of
sulfur, is described. It is stated that proportions of sulfur in the
catalyst are undesirably entrained in the dehydrogenation by the
reaction product or by escaping gas. The disadvantage of the process of
German Offenlegungsschrift No. 2β 27 421 is that selenium is also
entrained during the reaction and the catalyst is destroyed during
prolonged operation. A particular disadvantage is that sulfur and
selenium, especially in the form of their hydrogen acids, contaminate
the end product and cause environmental protection problems in the
exhaust gas. The contaminated end product creates corresponding
difficulties in its further processing. Overall, additional measures and
systems with regard to the processing, cleaning of the end product and
the exhaust gas as well as regulation and control of the systems will be
necessary.
2Q
It has now been found that formaldehyde advantageously obtained by the
dehydrogenation of methanol in the presence of a catalyst at elevated
temperature when the reaction is carried out in the presence of copper,
zinc, and tellurium-containing catalysts at a temperature of 0 C to 750 JJOO
25 will
The implementation can be represented by the following formulas:
30 CH 3 OH> CH 2 O + H 2
In
comparison to the known processes, the process according to the
invention surprisingly provides a simpler and more economical one
Ways formaldehyde in good yield and purity. With regard to the known
processes that lead to aqueous
130033/0344
'. ■' ■ '■ ; : ■: j 300AA36
BASF Aktiengesellschaft -Jf- OZ 0050/0 ^ 4274
lead r gene formaldehyde solutions obtained low-water, methanol Ί,
advantageously 10 to 40 percent strength by weight formaldehyde
solutions. The water content is usually less than 1.5 percent by weight,
mostly from 0.2 to 0.9 percent by weight, based on the total solution.
The catalyst has a significantly longer service life and activity,
usually over or equal to 80 operating hours compared to less or the same
10 operating hours in the case of copper / zinc / sulfur and less than
or equal to 40 operating hours in the case
^ q Copper / zinc / selenium as a catalyst for comparable sales.
The addition of hydrogen gas can surprisingly be saved
will. In view of the publications mentioned above, it was not to be expected that tellurium would occur in the reaction
is hardly removed from the catalyst. The content of the reaction
] 5
mixture of comparable conversions is usually
= 0.5 rag / kg tellurium, 3 to 175 mg / kg S for sulfur-containing and 5
to 8 ^ 0 mg / kg Se for selenium-containing catalysts. Corresponding
the process is more reliable and environmentally friendly and saves
additional control and cleaning operations,
Systems and frequent catalyst changes. All these beneficial results of
the invention
Process are in particular with regard to J. Falbe and U. Hasserodt,
catalysts, surfactants and mineral oil additives
(Thieme Verlag, Stuttgart 1978), page 67, surprising, since it is
expressly stated there that contacts for oxidation
from acrolein to acrylic acid using cobalt, molybdenum and tellurium
oxide precisely because of the volatility of the
Tellurs have not found any technical application.
Suitable starting materials for the process are pure methanol or technical-grade methanol. Also raw methanol, that
usually as described in DAS 12 77 8 ^ 4 and DP 12 35 88I
Process purified by treatment with oxidizing agents and / or alkalis can be used.
130033/0344
BASF Aktiengesellschaft -X- OZ 0050/034274
r The catalyst contains the metals preferably in an atomic ratio of 1 Ί
copper at 0.01 to 0.5, preferably 0.05 to 0.4 zinc and from 0.001 to
0.3, preferably 0.005 to 0.2 tellurium. An atomic ratio of 0.05 to 0.3
zinc to 1 copper and / or 0.005 to 0.1 tellurium to 1 c
The parts given in the following examples are parts by weight. They relate to the volume parts as
Kilograms to liters. Conversion and selectivity are defined in the following form:
converted methanol (mol)
Sales % = χ 100
] q supplied methanol (mol)
formaldehyde formed (mol)
Selectivity % = x. 100
converted methanol (mol)
15 Example 1
a)
Preparation of catalyst: 84 parts of copper (II) oxide, 11.8 parts of
zinc oxide and 4.2 parts of tellurium dioxide were mixed well with 50
parts ater V / mm dried at 130 0 C and pills of 3 mm diameter and 3 Processed height.
b) Reaction: parts by volume of the catalyst obtained in this way are placed in a tubular quartz glass reactor (0
3.2 cm). 132 parts / hour of methanol are evaporated, continuously
introduced into the reactor and reacted at a temperature of 550.degree.
The reaction mixture is condensed. 20.2 parts per hour (selectivity 76% of theory) of formaldehyde in addition to 0.5 parts of water are obtained
3Q ser, 79 parts of methanol. The turnover is 26 percent,
the proportion of entrained tellurium <0.5 mg / kg reaction mixture.
1 30033/0344 BATH ORIGINAL,
**********************************************************************************************************************
JPH078812B2
*
1986-09-24
1995-02-01
住友化学工業株式会社
Formaldehyde manufacturing methodDETAILED
DESCRIPTION OF THE INVENTION <Industrial Field of Application>
The present invention relates to a method for producing formaldehyde.
More
specifically, the present invention relates to a method for producing
formaldehyde, which comprises using a specific zinc-silicon composite
oxide as a catalyst for producing formaldehyde by dehydrogenating
methanol in the substantial absence of oxygen.
<Prior arts and problems to be solved by the invention>
Formaldehyde is used as a resin raw material such as polyacetal resin,
urea resin and phenol-formaldehyde resin, or a raw material for various
industrial chemicals such as pentaerythritol and hexamethylenetetramine.
It is an important basic raw material in the chemical industry.
As a
method for industrially producing formaldehyde, a method in which
methanol is subjected to catalytic oxidative dehydrogenation with a
silver catalyst under air flow, or a catalytic oxidation method using a
mixed catalyst of iron oxide and molybdenum oxide in place of the silver
catalyst is well known.
It is also well known that in such a method, a large amount of water is
produced as a by-product in addition to formaldehyde, and formaldehyde
is usually absorbed by water and collected, so that the product obtained
is an aqueous solution having a concentration of 30 to 50%. ing.
However, these methods have a drawback that complicated and expensive
equipments, large amounts of steam, power costs, etc. are required for
prevention of catalyst deactivation, removal of by-products, etc. Since
it is a water-containing product, it is necessary to remove a large
amount of water because it is necessary to remove a large amount of
water for raw materials in the field of dislike water, which is in great
demand in recent years, especially in the field of resins such as
polyacetal resin. It was also a problem in consuming.
In
order to solve the problems of the catalytic oxidative dehydrogenation
method and the catalytic oxidative method, various methods are also
available for the so-called catalytic dehydrogenation method, in which
formaldehyde is produced by dehydrogenating methanol in the substantial
absence of oxygen. Proposed.
For example, as a catalyst, a method using a catalyst composed of
copper, silver and silicon (Japanese Patent Publication No. 41-11853), a
method using molten zinc, gallium, indium, aluminum or the like
(Japanese Patent Publication No. 47-19251) Sho-48-97808), copper,
A method using a catalyst composed of zinc and sulfur or selenium
(JP-A-51-1407, 51-76209, 52-215) and the like have been proposed, all of
which include the yield of formaldehyde, the selectivity and the
catalyst. It was not possible to select the basic performance of the
catalyst such as the life at the same time.
The
present inventors have conducted various studies to solve the
above-mentioned problems of the catalytic dehydrogenation method of
methanol, and already used a metal oxide obtained by calcining a
specific zinc salt and / or indium salt as a catalyst, A method of using
a catalyst in which a zinc oxide and / or an indium oxide is supported
on silica has been proposed (JP-A-60-4147 and 60-6629).
The
present inventors have conducted extensive studies in order to find a
further excellent method for producing formaldehyde, and as a result, if
a catalyst made of a zinc-silicon composite oxide obtained by a
specific formulation is used,
Further, they have found that formaldehyde can be stably produced in a
high yield over a long period of time, and have reached the present
invention.
<Means for Solving Problems> That is, in the present invention,
when a formaldehyde is produced by dehydrogenating methanol in the
substantial absence of oxygen, a solution of a zinc compound and a
solution of an inorganic silicic acid compound are used as catalysts. An
industrially excellent method for producing formaldehyde characterized
by using a zinc-silicon composite oxide obtained by forming a
precipitate by mixing and then subjecting the precipitate to a
calcination treatment at a temperature of 500 ° C. or higher. Is
provided.
The
present invention is characterized by using a zinc-silicon composite
oxide obtained by the above-mentioned specific formulation as a
catalyst, but the content of zinc contained in the catalyst is usually 5
˜75 wt%, preferably 20 to 60 wt%, and the atomic ratio of silicon to zinc is usually 1/10 to 10/1.
DE919227C
*
1943-08-06
1954-10-18
Rheinpreussen Ag
Process for the preparation of zinc oxide catalysts for the dehydrogenation of secondary alcohols to ketones
JPS511407A
*
1974-06-07
1976-01-08
Mitsubishi Gas Chemical Co
Horumuarudehidono seizohoho
JPS52215A
*
1975-06-20
1977-01-05
Mitsubishi Gas Chem Co Inc
Process for preparation of formaldehyde
JPS5412444A
*
1977-06-30
1979-01-30
Nichicon Capacitor Ltd
Film capacitor
US4371730A
*
1981-06-05
1983-02-01
Phillips Petroleum Company
Dehydrogenation of organic compounds with a zinc silicate catalyst
DE3470031D1
*
1983-06-23
1988-04-28
Sumitomo Chemical Co
A process for producing formaldehyde
JPH062698B2
*
1985-07-23
1994-01-12
住友化学工業株式会社
Formaldehyde production method
JPH062699B2
*
1986-06-09
1994-01-12
住友化学工業株式会社
Formaldehyde production method
* Cited by examiner, † Cited by third party
Publication number
Priority date
Publication date
Assignee
Title
DE3920811A1
*
1989-06-24
1991-01-03
Hoechst Ag
METHOD FOR PRODUCING FORMALDEHYDE
US5103058A
*
1990-11-05
1992-04-07
Exxon Chemical Patents Inc
Process for producing imines and/or amines from alcohols
GB9812083D0
1998-06-05
1998-08-05
Ici Plc
Removal of water
GB202206338D0
*
2022-04-29
2022-06-15
Johnson Matthey Plc
Stabilised zinc oxide materials
* Cited by examiner, † Cited by third party, ‡ Family to family citation
***************************************************************************************************
DE3920811A1
*
1989-06-24
1991-01-03
Hoechst Ag
METHOD FOR PRODUCING FORMALDEHYDE
worked MeOH diluted in Nitrogne
Description
translated from German
The
present invention relates to a method for Production of formaldehyde by
dehydration of methanol in the presence of a catalyst at elevated
temperature.
There are several methods of making formaldehyde
known from methanol. In technology, the oxidation of Methanol to
formaldehyde is common
CH₃OH + 1/2 O₂ → CH₂O + H₂O
the
catalysts containing iron and molybdenum oxide is carried out at 350 °
C to 450 ° C. It is also common the oxidative dehydrogenation of
methanol to formaldehyde.
CH₃OH ⇄ CH₂O + H₂
H₂ + 1/2 O₂ ⇄ H₂O
on
silver catalysts at 600 to 720 ° C. Both procedures are described in
Ullmann's Encycl. the technical Chemistry, Volume 11, pp. 693-694, 4th
edition, 1976, Verlag Chemie Weinheim.
For example, a method for
producing Formaldehyde from methanol by increased dehydration Known
temperature at which the reaction in the presence one containing at
least one sodium compound Catalyst at a temperature of 300 ° C to 800 °
C is carried out (DE-A 37 19 055).
Another publication, in which the
use of a catalyst containing silver oxide is mentioned, states that
care must be taken to ensure the absence of Al 2 O 3 and MgO as an
impurity (JP-A 60 089-441 = Derwent Report 85-1 56 891/26).
However,
the known catalysts do not allow economical production of formaldehyde
by dehydration of methanol. In the known methods, the Yields of
formaldehyde less than 70% in all cases and sales, i.e. the ratio of
converted methanol added methanol was never greater than 95%.
The
invention therefore relates to a method for manufacturing of
formaldehyde by dehydration of methanol in the presence a catalyst at
elevated temperature, the Implementation at a temperature of 650 to
1050 ° C below Exclusion of oxygen in the presence of aluminum oxide,
Alkali aluminate and / or alkaline earth aluminate as a catalyst in a
reactor, the inner wall of which is wholly or partly made Alumina is
made.
The reaction can be done through the equation
CH₃OH ⇄ CH₂O + H₂
to be discribed.
The process surprisingly supplies formaldehyde good selectivity and yield.
Are
suitable for the preparation of the catalyst Aluminum compounds such as
the oxides, hydroxides, carbonates, Bicarbonates, oxalates, acetates or
nitrates alone or in Mixture with appropriate alkali or alkaline earth
compounds. Coming as cations of the alkali and alkaline earth compounds
those of the 1st and 2nd main group of the periodic table in Question
like lithium, sodium, potassium, rubidium, magnesium, Calcium,
strontium and barium, but preferably lithium and sodium or
mixtures thereof. The catalyst can used in a technically common form
for example in the form of balls or sticks. He can immediately, i.e. in
the initial form of the connections are used or previously thermally,
for example the air and / or chemically activated. In any Case, the
starting compounds at the high Temperatures in the reactor converted
into the active form. Anionic groups such as carbonate, bicarbonate,
oxalate, acetate or nitrate after treatment at temperatures, which
correspond to the reaction temperatures, no longer proven.
The
reaction temperatures during the dehydrogenation of the methanol are
generally 650 to 1050 ° C, preferably 820 to 950 ° C and especially 850
to 920 ° C. The one in the process prevailing pressure is not critical.
The dehydration of the Methanol can with negative pressure, normal
pressure or positive pressure, but preferably carried out at a pressure
of about 1.2 bar will.
The methanol, which is in gaseous state in
the reactor, can as such or with carbon dioxide, if necessary also
mixed with an inert gas, preferably nitrogen to be implemented. It can
also contain water be added to the reaction mixture. The added
Connections have a positive effect on long-term activity of the
catalyst, since these substances of deactivation counteract the
catalyst. Generally until 1% by weight of water and / or up to 3 mol%
of carbon dioxide, in each case based on the metered amount of methanol
used.
The process according to the invention can be carried out
batchwise, but preferably be carried out continuously. Here 0.1 to 100
kg, preferably 0.5 to 10 kg, of methanol per hour and per kilogram of
catalyst.
The measurands given in the examples were as calculated as follows:
A
minor formation of carbon monoxide occurred as a side reaction on. When
carrying out the process, in the water to Reaction mixture was added
were in the product gas small amounts of carbon dioxide and methane
were found. In in no case could water, not even that Reaction mixture
metered in, detected in the product gas will.
Examples
1)
Sodium carbonate and aluminum hydroxyacetate were mixed so that one
mole of aluminum was replaced by one mole of sodium. The mixture was
calcined in air at 900 ° C for 3 days. The product thus obtained was
triturated and pressed into pellets with a diameter of 6 mm. These were
crushed and a grain fraction of 2 mm ħ 1 mm in diameter was selected.
1.71 g of the catalyst thus obtained with a bulk volume of 2.2 ml were
placed in a tube made of Al 2 O 3 with an inner diameter of 12 mm. The
metered methanol contained 0.1 percent by weight of water. At a
reaction temperature of 900 ° C. and an inlet of 3.97 mol / h (10 mol%
of methanol, remainder nitrogen (N 2 )), the conversion of methanol was
100% and the yield of formaldehyde was 69.4%.
2) Lithium
carbonate and aluminum nitrate were mixed so that one mole of lithium
accounted for one mole of aluminum. The mixture was calcined in air for
1 1/2 days. The catalyst thus obtained was pressed into pellets with a
diameter of 6 mm. These were crushed and a grain fraction with a
diameter of 1 mm ħ 0.5 mm was selected. 0.75 g of this substance with a
bulk volume of 1 ml was placed in an Al 2 O 3 tube with an inner
diameter of 12 mm. The metered in methanol contained 0.05 percent by
weight of water. At a reaction temperature of 850 ° C. and a feed rate
of 3.97 mol / h (10 mol% of methanol, balance N 2 ), the conversion of
methanol was 49.2% and the yield of formaldehyde was 23.9%.
************************************************************************************************
EP0261867B1 Process for producing formaldehyde
Current Assignee Sumitomo Chemical Co Ltd
Worldwide applications
1986
JP
1987
EP
DE
US
Description
- [0001]
The
present invention relates to a process for producing formaldehyde. More
particularly, it is concerned with an improved process for producing
formaldehyde by dehydrogenation of methanol in the substantial absence
of oxygen, in which the catalyst is a specific zinc-silicon complex
oxide.
- [0002]
Formaldehyde
is an important basic raw material in the chemical industry. It is used
for the production of synthetic resins such as polyacetal resin, urea
resin, and phenol-formaldehyde resin; and chemicals such as
pentaerythritol and hexamethylenetetramine.
- [0003]
Formaldehyde
is commercially produced from methanol by the silver-catalyzed
oxidation-dehydrogenation in an air flow, or by a catalytic oxidation
process which employs a mixture of iron oxide and molybdenum oxide as a
catalyst in place of silver.
These processes, however, have some disadvantages. First, they need a
complex and expensive equipment to protect the catalyst from
deactivation and to remove by-products, and they also consume a large
amount of steam and power. Secondly, they produce a large amount of
water as a by-product and they produce formaldehyde in the form of 30 -
50% aqueous solution because the resultant formaldehyde is recovered by
absorption into water. A large amount of water in the aqueous solution
has to be removed in an instance where formaldehyde is used for the
production of polyacetal resin, and this leads to a high energy cost.
- [0004]
In
order to eliminate the disadvantages of the catalytic
oxidation-dehydrogenation process and catalytic oxidation process, there
have been proposed several catalytic dehydrogenation processes, by
which formaldehyde is produced by dehydrogenating methanol in the
substantial absence of oxygen.
The catalyst varies from one process to another. For example, in the
process disclosed in Japanese Patent Publication No. 11853/1966, the
catalyst is composed of copper, silver, and silicon; in the process
disclosed in Japanese Patent Publication No. 19251/1972 and Japanese
Patent Laid-open No. 97808/1983, the catalyst is molten zinc, gallium,
indium, or aluminum; and in the process disclosed in Japanese Patent
Laid-open Nos. 1407/1976, 76209/1976, and 215/1977, the catalyst is
composed of copper, zinc, and sulfur or selenium. However, none of these
catalysts are satisfactory in all of the basic performances required
for catalysts such as yield, selectivity and life.
- [0005]
In
order to address the above-mentioned problems involved in the catalytic
dehydrogenation of methanol, the present inventors carried out a series
of researches which matured into their previous inventions relating to a
process which employs as a catalyst a metal oxide obtained by burning a
specific zinc salt and/or indium salt, and a process which employs as a
catalyst zinc oxide and/or indium oxide carried on silica. They are
disclosed in Japanese Patent Laid-open No. 4147/1985 and Japanese Patent
Publication No. 6629/1985.
- [0006]
As
the result of their continued studies in search of an improved process
for the production of formaldehyde, the present inventors have found
that a catalyst composed of zinc-silicon complex oxide of specific
composition permits the stable production of formaldehyde with high
yield over a long period of time. The present invention is based on this
finding.
- [0007]
It
is an object of the present invention to provide an economically
advantageous process for producing formaldehyde by dehydrogenating
methanol in the substantial absence of oxygen, said process being
characterized in that the dehydrogenation is performed by the aid of a
catalyst which is a zinc-silicon complex oxide obtained by mixing a
solution containing a zinc salt of an inorganic or organic acid with a
solution containing an inorganic silicate compound, or by adding urea to
a solution containing a zinc salt of an inorganic or organic acid and
an organic silicate compound, thereby forming a precipitate, and
subsequently baking the precipitate at 500°C or higher.
- [0008]
According
to the present invention, the catalyst used in the process is a
zinc-silicon complex oxide of specific composition. An amount of zinc in
the catalyst should be 5 - 75 wt%, preferably 20 - 60 wt%, and an
amount of silicon in the catalyst should be in the range defined by the
silicon-to-zinc atomic ratio of 1/10 to 10/1.
- [0009]
The
zinc moiety of the catalyst may be obtained from a variety of zinc
salts. They include zinc salts of inorganic acids such as nitrate and
sulfate and zinc salts of organic acids such as carboxylates. Preferable
among them are zinc nitrate and zinc carboxylate.
- [0010]
The
silicon moiety of the catalyst may be obtained from a variety of
inorganic silicates such as sodium silicate, potassium silicate, and
ammonium silicate, and organic silicates exemplified below. Ammonium
silicate is most desirable among inorganic silicates because it does not
contain any alkali that might remain in the catalyst.
- [0011]
The organic silicates are ortho-silicates represented by the formula (I).
where Rı, R², R³, and R⁴ independently represent alkyl, alkenyl,
alkynyl, aryl, aralkyl or organic carbonyl; and n is an integer from 1
to 10.
- [0012]
Examples
of Rı, R², R³, and R⁴ include alkyl such as methyl, ethyl, n-propyl,
i-propyl, n-butyl, i-butyl, sec-butyl, pentyl, cyclopentyl, hexyl, and
cyclohexyl; alkenyl such as vinyl, propenyl, allyl, isopropenyl, and
cyclohexenyl; alkynyl such as ethynyl and 2-propynyl; aryl such as
phenyl, tolyl, and xylyl; aralkyl such as benzyl; and organic carbonyl
such as formyl, acetyl, and propionyl.
- [0013]
Examples
of the organic silicates include tetraalkyl silicates such as
tetramethoxysilane and tetraethoxysilane and condensates thereof.
- [0014]
In
the preparation of the catalyst, aqueous solution of the
above-mentioned zinc salt and aqueous solution of the above-mentioned
inorganic silicate are mixed together to form a precipitate. The mixing
may be accomplished by adding the former to the latter, by adding the
latter to the former, or by adding the both to each other
simultaneously. The precipitation may be accomplished by controlling the
pH with an acid (e.g., sulfuric acid and acetic acid) or an alkali
(e.g., ammonia and sodium carbonate). The precipitation may be
accomplished at any temperature, usually at room temperature.
- [0015]
In
the case where aqueous solution of zinc salt and aqueous solution of
organic silicate are used, precipitation is accomplished by the aid of
urea as a precipitant. Any commercial urea suffices. The urea is used in
an amount of 1 - 20 mol, preferably 2 - 10 mol, for 1 mol of zinc.
- [0016]
Only
for the purpose of precipitation, the urea may be replaced by an alkali
such as sodium hydroxide, potassium hydroxide, potassium hydrogen
carbonate, sodium carbonate, sodium hydrogen carbonate, and ammonia,
which is commonly used as a precipitant for metal ions. However, such an
alkali precipitant provides a catalyst having a very small activity.
However, the urea precipitant provides a catalyst which has not only an
extremely large activity but also a longer life compared with any known
catalysts.
- [0017]
The
function of the urea is not fully elucidated yet. The fact that urea
provides a catalyst having an extremely large specific surface area
(measured by the BET method) suggests that urea causes the formation of
zinc hydroxide and the hydrolysis of organic silicate to proceed
simultaneously, thereby forming a precipitate of uniform composition.
- [0018]
The
preparation of the catalyst from an organic silicate is carried out in
the following manner. At first, a precursor of the zinc oxide and an
organic silicate are dissolved in alcohol or water or a mixture thereof.
In the resulting solution is dissolved urea. Subsequently, the solution
is heated at 60 - 150°C for 1 - 100 hours to bring about precipitation.
- [0019]
The
precipitate formed in the above-mentioned manner is filtered off,
washed, and dried. It is finally baked in an air stream or an inert gas
stream at 500 -1200°C, preferably 600 - 1100°C, and more preferably
about 900 - 1000°C. Thus there is obtained a catalyst which is
characterized by that very little zinc is lost by reduction during
reaction. The baking at about 900 - 1000°C affords a catalyst which
maintains the activity for an extremely long period of time, with almost
no loss of zinc. Presumably, this is because the baking at that
temperature forms crystalline zinc silicate (Zn₂SiO₄).
- [0020]
The
catalyst obtained as mentioned above is used for the dehydrogenation of
methanol which is usually performed in a flowing gas reaction system.
In this reaction system, methanol is supplied in a gaseous form to the
catalyst layer, which is usually kept at 450 -650°C, preferably 450 -
550°C. The reaction may be carried out under any pressure, usually
atmospheric pressure to 10 kg/cm².
- [0021]
Feed
methanol may be diluted with an inert gas (e.g., nitrogen, methane,
carbon dioxide) and/or hydrogen. Methanol should be fed at a rate of 0.1
-10 kg/hr per kg of catalyst, depending on the volume and shape of the
reactor. With a feed rate of less than 0.1 kg/hr, the reaction is not
practical, and with a feed rate of more than 10 kg/hr, the conversion of
methanol is small.
- [0022]
The
product gas discharged from the reactor is cooled and then introduced
to a heat-exchanger type condenser or an absorbing tower for the
recovery of formaldehyde. Incidentally, the product gas contains water
in a very small amount, say 0.01 mol or less for 1 mol of formaldehyde.
This makes the process advantageous for the production of water-free
high-purity formaldehyde. In the case where the absorbent is a higher
alcohol such as polyethylene glycol, diethylene glycol, and
cyclohexanol, formaldehyde is recovered in the form of hemiformal
solution of higher alcohol. Upon thermal decomposition, it readily
provides high-purity formaldehyde.
- [0023]
According
to the process of the invention, the catalyst permits the production of
formaldehyde in a high yield at a high conversion of methanol.
Moreover, blocking of a catalyst and loss of zinc by reduction are so
greatly controlled that production of formaldehyde is ensured for a long
period of time with high yield. In addition the process of the
invention provides formaldehyde containing a very small amount of water
which is able to remove easily. The formaldehyde is especially suitable
for the production of polyacetal and oil-soluble phenolic resin, in
which contamination of water should be avoided. The production of
formaldehyde by the process of this invention also affords a large
amount of hydrogen (offgas) which can be effectively utilized as a heat
source or feedstock.
- [0024]
The
present invention, owing to the above-mentioned advantages, is also
able to apply to the production of aldehydes or ketones through the
dehydrogenation of the corresponding alcohols other than methanol, such
as ethanol, butanol, isopropanol, and cyclohexanol.
- [0025]
The following examples will be helpful to further understand the invention.
(I) Preparation of Catalysts
Catalyst-A
- [0026]
Solution-A
(aqueous solution of ammonium silicate (NH₄)₂SiO₃) was prepared by
passing an aqueous solution of sodium silicate (15.3g of Na₂SiO₃·9H₂O in
100 ml of distilled water) at a flow rate of 500 ml/min through a
column filled with 400 ml of ion-exchange resin (Duorite C-22) which had
previously been ion-exchanged into NH₄-type.
- [0027]
Solution-B
(aqueous solution of zinc nitrate) was prepared by dissolving 37.2g of
zinc nitrate Zn(NO₃)₂·6H₂O in 100 ml of distilled water.
- [0028]
The
solution-A was added dropwise with thorough stirring over 30 minutes to
the solution-B which was heated at 60°C. After the addition, stirring
was continued for additional 30 minutes. The resulting white slurry was
filtered and the separated solids were washed with water and dried at
150°C for 12 hours. The solids were baked at 340°C for 2 hours in the
air and further baked at 600°C for 5 hours in an electric furnace. Thus
there was obtained Catalyst-A.
- [0029]
Catalyst-A
contains 43.1 wt% of zinc and 21.2 wt% of silicon, and has a specific
surface area of 222.6 m²/g (measured by the BET method). In addition,
Catalyst-A contains amorphous SiO₂ and ZnO according to X-ray
diffractometry.
Catalyst-B
- [0030]
A
white slurry was prepared according to the same procedure as in the
production of Catalyst-A. The slurry was filtered and the separated
solids were washed with water and dried at 150°C for 12 hours. Using an
electric furnace, the solids were baked at 350°C for 2 hours in the air
and further baked at 1000°C for 5 hours. Thus there was obtained
Catalyst-B.
- [0031]
Catalyst-B
contains 43.1 wt% of zinc and 21.2 wt% of silicon, and has a specific
surface area of 40.8 m²/g (measured by the BET method). In addition,
Catalyst-B contains amorphous Zn₂SiO₄ alone according to X-ray
diffractometry.
Catalyst-C
- [0032]
Solution-B
(aqueous solution of zinc nitrate) was prepared by dissolving 37.2g of
zinc nitrate Zn(NO₃)₂·6H₂O in 100 ml of distilled water.
- [0033]
Solution-C
(aqueous solution of sodium metasilicate Na₂SiO₃·6H₂O) was prepared by
dissolving 15.3g of sodium metasilicate in 100ml of distilled water.
- [0034]
The
solution-C was added dropwise with thorough stirring over 30 minutes to
the solution-B which was heated at 60°C. After the addition, stirring
was continued for further 30 minutes. The resulting white slurry was
filtered and the separated solids were washed with water and dried at
150°C for 12 hours. Using an electric furnace, the solids were baked at
350°C for 2 hours in the air and further baked at 600°C for 5 hours.
Thus there was obtained Catalyst-C.
- [0035]
Catalyst-C
contains 42.6 wt% of zinc and 21.5 wt% of silicon, and has a specific
surface area of 138.0 m²/g (measured by the BET method). In addition,
Catalyst-C contains amorphous SiO₂ and ZnO according to X-ray
diffractometry.
Catalyst-D
- [0036]
In
a mortar, 10g of commercial zinc oxide ZnO and 7.48g of silicon dioxide
were thoroughly mixed. Using an electric furnace, the mixture was baked
at 350°C for 2 hours in the air and further baked at 1000°C for 5
hours. Thus there was obtained Catalyst-D.
- [0037]
Catalyst-D
contains 46.0 wt% of zinc and 20.0 wt% of silicon, and has a specific
surface area of 91.1 m²/g (measured by the BET method).
Catalyst-E
- [0038]
In
a mortar, 20g of commercial zinc oxide ZnO and 7.48g of silicon dioxide
were thoroughly mixed. Using an electric furnace, the mixture was baked
at 350°C for 2 hours in the air and further baked at 1000°C for 5
hours. Thus there was obtained Catalyst-E.
- [0039]
Catalyst-E
contains 58.8 wt% of zinc and 12.7 wt% of silicon, and has a specific
surface area of 62.5 m²/g (measured by the BET method).
Catalyst-F
- [0040]
A half of Catalyst-D was baked at 1300°C for 3 hours in the air to give Catalyst-F.
- [0041]
Catalyst-F
contains 46.0 wt% of zinc and 20.0 wt% of silicon, and has a specific
surface area of 0.6 m²/g (measured by the BET method).
Catalyst-G
- [0042]
A half of Catalyst-E was further baked at 1300°C for 3 hours in the air to give Catalyst-G.
- [0043]
Catalyst-G
contains 58.8 wt% of zinc and 12.7 wt% of silicon, and has a specific
surface area of 0.3 m²/g (measured by the BET method).
Catalyst-H
- [0044]
Solution-C
(aqueous solution of zinc nitrate) was prepared by dissolving 14.6g of
zinc nitrate Zn(NO₃)₂·6H₂O in 200 ml of distilled water. To solution-C
was added 20g of silicon dioxide. The resulting slurry mixture was
thoroughly mixed on a water bath at 80°C for 1 hour, and subsequently
dried under reduced pressure in a rotary evaporator. The resulting
solids were baked at 350°C for 2 hours in the air and further baked at
600°C for 5 hours in an electric furnace. Thus there was obtained
Catalyst-H.
- [0045]
Catalyst-H
contains 12.9 wt% of zinc and 38.0 wt% of silicon, and has a specific
surface area of 75.0 m²/g (measured by the BET method).
Catalyst-I
- [0046]
The
same procedure as in the preparation of Catalyst-H was repeated to give
Catalyst-I, except that the baking at 600°C for 5 hours was changed to
1000°C for 5 hours.
- [0047]
Catalyst-I
contains 12.9 wt% of zinc and 38.0 wt% of silicon, and has a specific
surface area of 125.0 m²/g (measured by the BET method).
Catalyst-J
- [0048]
Solution-C
(aqueous solution of zinc nitrate) was prepared by dissolving 7.4g of
zinc nitrate in 200 ml of distilled water. To solution-C was added 25g
of silica sol (trade name "Snowtex N", containing 20 wt% of SiO₂). The
resulting slurry mixture was thoroughly mixed on a water bath at 80°C
for 1 hour, and subsequently dried under reduced pressure in a rotary
evaporator. The resulting solids were baked at 350°C for 2 hours in the
air and further baked at 600°C for 5 hours in an electric furnace. Thus
there was obtained Catalyst-J.
- [0049]
Catalyst-J
contains 12.9 wt% of zinc and 38.0 wt% of silicon, and has a specific
surface area of 135.6 m²/g (measured by the BET method).
Catalyst-K
- [0050]
A half of Catalyst-J was further baked at 1000°C for 3 hours in the air to give Catalyst-K.
- [0051]
Catalyst-K
contains 12.9 wt% of zinc and 38.0 wt% of silicon, and has a specific
surface area of 65.89 m²/g (measured by the BET method).
Catalyst-L
- [0052]
In
100g of ethanol was dissolved 23.93g of zinc nitrate Zn(NO₃)₂·6H₂O. To
the resulting solution was added 16.66g of tetraethoxysilane, followed
by stirring for 30 minutes at room temperature. To the solution was
added urea solution (28.8g of urea in 84.6g of distilled water),
followed by stirring at room temperature for 30 minutes. The solution
temperature was raised to 80°C with stirring, and stirring was continued
at that temperature for 9 hours to give a white slurry liquid. After
being filtered and washed with water, the white solids were dried at
150°C for 12 hours. The dried solids were baked at 350°C for 2 hours in
the air and further baked at 600°C for 5 hours in an electric furnace.
Thus there was otbained Catalyst-L.
- [0053]
Catalyst-L
contains 36.2 wt% of zinc and 25.5 wt% of silicon, and has a specific
surface area of 296.5 m²/g (measured by the BET method).
Catalyst-M
- [0054]
The
same procedure as in the preparation of Catalyst-L was repeated to give
Catalyst-M, except that the urea solution was replaced by 58.3g of 28
wt% ammonia water which was added dropwise with stirring over 30
minutes.
- [0055]
Catalyst-M
contains 34.6 wt% of zinc and 24.5 wt% of silicon, and has a specific
surface area of 6.6 m²/g (measured by the BET method).
Catalyst-N
- [0056]
In
39.5g of ethanol was dissolved 53.4g of zinc nitrate Zn(NO₃)₂·6H₂O. To
the resulting solution were added 37.2g of tetraethoxysilane dissolved
in 39.5g of ethanol, followed by stirring for 30 minutes at room
temperature. To the solution was added urea solution (61.5g of urea in
150g of distilled water), followed by stirring at room temperature for
30 minutes. The solution temperature was raised to 80°C with stirring,
and stirring was continued at that temperature for 6 hours to give a
white slurry liquid. After being filtered and washed with water, the
white solids were dried at 150°C for 12 hours. The dried solids were
baked at 350°C for 2 hours in the air and further baked at 600°C for 1
hour in an electric furnace. Thus there was obtained Catalyst-N.
- [0057]
Catalyst-N
contains 44.6 wt% of zinc and 19.5 wt% of silicon, and has a specific
surface area of 225 m²/g (measured by the BET method).
Catalyst-O
- [0058]
The
same procedure as in the preparation of Catalyst-N was repeated to give
Catalyst-O, except that the amount of zinc nitrate was 26.7g in place
of 53.4g, the amount of urea 30.7g in place of 61.5g, and the amount of
distilled water (as a solvent of urea) 170g in place of 150g.
- [0059]
Catalyst-O
contains 31.3 wt% of zinc and 27.7 wt% of silicon, and has a specific
surface area of 371 m²/g (measured by the BET method).
Catalyst-P
- [0060]
In
200 ml of water was dissolved 18.27g of zinc nitrate Zn(NO₃)₂·6H₂O. To
the resulting solution was added 25g of silica sol (tradename "Snowtex
N" produced by Nissan Kagaku Co., Ltd. containing 20 wt% of SiO₂). The
resulting slurry mixture was thoroughly mixed on a water bath at 80°C
for 1 hour, and subsequently dried under reduced pressure in a rotary
evaporator. The resulting solids were baked at 350°C for 2 hours in the
air and further baked at 600°C for 5 hours in an electric furnace Thus
there was obtained Catalyst-P.
- [0061]
Catalyst-P
contains 40.2 wt% of zinc and 23.4 wt% of silicon, and has a specific
surface area of 78 m²/g (measured by the BET method).
- [0062]
The above-mentioned catalysts A to P were granulated into 24 - 48 mesh particles. They were stored in a desiccator.
- [0063]
The
specific surface area was measured with "Monosorb" (tradename made by
Quantachrome) after dehydration in a nitrogen stream at 200°C for 30
minutes.
(II) Catalyst reaction test- [0064]
To
evaluate the catalysts prepared as mentioned above, the dehydrogenation
of methanol was carried out by passing a methanol-nitrogen mixture
(CH₃OH/N₂ = 18/32 in mol), which had previously been vaporized at 150°C,
through a tubular quartz reactor, 10 mm in inside diameter, filled with
1.0g of the sample catalyst. The reaction temperature was 520 - 550°C
and the flow rate was 550 mmol/hr under atmospheric pressure.
- [0065]
A
gas from the reactor was subjected, by means of a heat-insulated gas
sampler, to a gas chromatography (thermal conductivity detector)
equipped with a 6-m column (APS-201, 20% Fulsin T, made by Gasukuro
Kogyo Inc.) and a 2-m column (molecular sieve 13x), to effect
quantitative analysis of formaldehyde [HCHO], methyl formate, dimethyl
ether, hydrogen [H₂] , carbon monoxide [CO], methane [CH₄], unaltered
methanol [CH₃OH at the exit] , and nitrogen. The results are shown in
Tables 1 and 2. (The gas chromatography detected almost no methyl
formate and dimethyl ether.)
- [0066]
Conversion
rate of methanol, yield of formaldehyde, and selectivity of
formaldehyde are calculated according to the following equations.
where [HCHO],[CO], [CH₄], and [DME] represent the rate (mmol/hr) at
which the respective components are formed, and [CH₃OH] represents the
flow rate (mmol/hr) of unaltered methanol measured at the exit of the
reactor tube.
-
Publication number
Priority date
Publication date
Assignee
Title
DE919227C
*
1943-08-06
1954-10-18
Rheinpreussen Ag
Process for the preparation of zinc oxide catalysts for the dehydrogenation of secondary alcohols to ketones
JPS511407A
*
1974-06-07
1976-01-08
Mitsubishi Gas Chemical Co
Horumuarudehidono seizohoho
JPS52215A
*
1975-06-20
1977-01-05
Mitsubishi Gas Chem Co Inc
Process for preparation of formaldehyde
JPS5412444A
*
1977-06-30
1979-01-30
Nichicon Capacitor Ltd
Film capacitor
US4371730A
*
1981-06-05
1983-02-01
Phillips Petroleum Company
Dehydrogenation of organic compounds with a zinc silicate catalyst
DE3470031D1
*
1983-06-23
1988-04-28
Sumitomo Chemical Co
A process for producing formaldehyde
JPH062698B2
*
1985-07-23
1994-01-12
住友化学工業株式会社
Formaldehyde production method
JPH062699B2
*
1986-06-09
1994-01-12
住友化学工業株式会社
Formaldehyde production method
* Cited by examiner, † Cited by third party
Publication number
Priority date
Publication date
Assignee
Title
DE3920811A1
*
1989-06-24
1991-01-03
Hoechst Ag
METHOD FOR PRODUCING FORMALDEHYDE
US5103058A
*
1990-11-05
1992-04-07
Exxon Chemical Patents Inc
Process for producing imines and/or amines from alcohols
GB9812083D0
1998-06-05
1998-08-05
Ici Plc
Removal of water
GB202206338D0
*
2022-04-29
2022-06-15
Johnson Matthey Plc
Stabilised zinc oxide materials
* Cited by examiner, † Cited by third party, ‡ Family to family citation
********************************************************************************************************************************
*************************************************************************************
CN111217683A
*
2018-11-27
2020-06-02
中国科学院大连化学物理研究所
Method for preparing anhydrous formaldehyde by methanol dehydrogenation
CN1103244C
*
1999-08-09
2003-03-19
中国石油化工集团公司
Novel load silver catalyst and preparation process thereof
US6563006B2
2001-04-30
2003-05-13
Melvin K. Carter
Catalytic oxidative conversion of hydrocarbons to aldehydes
CN105597756A
*
2016-03-02
2016-05-25
中国科学院山西煤炭化学研究所
Copper-based
core-shell catalyst for preparing methyl formate through methyl alcohol
dehydrogenation and preparation method and application thereof
CN111215062A
*
2018-11-27
2020-06-02
中国科学院大连化学物理研究所
Method for preparing anhydrous formaldehyde
*************************************************************************************************************
CN111217683A
*
2018-11-27
2020-06-02
中国科学院大连化学物理研究所
Method for preparing anhydrous formaldehyde by methanol dehydrogenation
Current Assignee Dalian Institute of Chemical Physics of CAS
Abstract
The
invention relates to a method for preparing anhydrous formaldehyde by
methanol dehydrogenation. The method adopts a palladium-indium catalyst
(PdIn/SiO) supported by silicon dioxide2) The specific process is as follows: PdIn/SiO2Filling
the formed catalyst into a reaction tube, then filling the reaction
tube into a fixed bed reactor, injecting methanol by an advection pump
under normal pressure, taking inert gas as carrier gas, wherein the
methanol feeding ratio is 10-60 vol%, and the methanol feeding speed is
0.10-0.30 mL/(g)cat.Min),
reacting at 350-600 ℃, and obtaining the conversion rate of the methanol
of 60-80% and the selectivity of the formaldehyde of 65-85% by
chromatography. The invention relates to a method for preparing
anhydrous formaldehyde by methanol dehydrogenation, which adopts
PdIn/SiO2As the catalyst, the
catalyst has higher catalytic activity and product selectivity, less
by-products, simple preparation process and high thermal stability.
Background
Formaldehyde
is an important organic chemical raw material, can be used for
producing thermosetting resins such as phenolic resin and melamine
resin, and bulk chemicals such as polyformaldehyde, phenolic aldehyde,
urotropine and 1, 4-butanediol, and is also a raw material for
synthesizing products such as dye, pesticide, disinfectant and adhesive.
At
present, the methanol oxidation method is generally adopted
industrially to prepare formaldehyde, theoretically, a formaldehyde
aqueous solution with the molar ratio of 1:1 is obtained, the vapor
pressure of the formaldehyde aqueous solution is low, the formaldehyde
and water form an azeotrope, the separation and purification of the
formaldehyde are very difficult, and the energy consumption is huge. In
recent years, the demand of engineering plastics, urotropine and other
medicines with excellent synthesis performance on anhydrous formaldehyde
is increasing, and the anhydrous formaldehyde is obtained by removing
moisture from industrial formaldehyde aqueous solution at present, so
that the direct preparation of the anhydrous formaldehyde is a hot point
of research.
The
process for preparing formaldehyde by anaerobic dehydrogenation of
methanol obtains formaldehyde and byproduct hydrogen, the formaldehyde
and the byproduct hydrogen are easy to separate, and the hydrogen is
industrial gas with high added value; the process has no water
generation, avoids the separation operation of the formaldehyde aqueous
solution, and greatly saves the purchase cost and the operation cost of
the rectification equipment; the process also avoids the problem that
the formic acid generated by the methanol oxidation method corrodes
equipment. Therefore, the direct dehydrogenation of methanol to prepare
formaldehyde is a process with great industrial prospect.
In
recent years, a new anhydrous formaldehyde preparation process with
remarkable economic benefit draws high attention at home and abroad, and
a great deal of research work is brought forward. Research efforts are
currently focused on the development of highly efficient catalysts,
including metals and their oxides, alkali metal salts, and molecular
sieves, among others. CN102274722A discloses a new type V2O3And a load type V2O3The
preparation method shows better activity in the dehydrogenation
reaction of methanol. Takagi et al (Takagi K, Morikawa Y, Ikawa
T.Chemestryletters, 1985, 14: 527-0Has
high selectivity to formaldehyde. CN101961650A discloses a homogeneous
coprecipitation method for preparing zirconium-based catalyst and
catalyzing methanol to perform anaerobic dehydrogenation, wherein the
yield of formaldehyde reaches 60%. Davirin et al (CN1390639A,
CN1537673A, CN1544147A) disclose a series of preparation methods of
silver-based catalysts for direct dehydrogenation of methanol. The
patent CN101147872A takes industrial sodium bicarbonate as a raw
material to prepare the anhydrous formaldehyde by catalyzing and
preparing the industrial sodium carbonate, and lays a foundation for the
industrialization of preparing the formaldehyde by methanol
dehydrogenation. Music et al (Music A, Batista J, Levec J.
appliedCatalysis A: general, 1997, 165: 115-131) takes a ZSM-5 molecular
sieve catalyst as a matrix, and prepares Na-ZSM-5 and Cu-ZSM-5 type
molecular sieves by an ion exchange method, thereby obtaining better
selectivity in the methanol dehydrogenation reaction. CN105601487A
discloses a rare earth complex Ln [ CH ]2(CH2)nR]3·xH2O.yL, the catalyst has higher selectivity to formaldehyde.
Based
on the above, the disadvantages of the catalysts currently used for the
preparation of anhydrous formaldehyde are: copper particles in the
copper-based catalyst are distributed unevenly, are larger, have smaller
active surface area and lower activity; the modified molecular sieve
catalyst is difficult to regulate and control in acid-base property and
has more byproducts; the catalytic activity of conventional carbonates
or bicarbonates is relatively inert and the reaction temperature is
generally above 700 ℃. The complex catalyst is a homogeneous catalysis
process, and the separation energy consumption is large. Therefore, a
heterogeneous catalytic system with good stability, high activity and
formaldehyde selectivity and mild reaction conditions is developed, and
the preparation of anhydrous formaldehyde by methanol dehydrogenation is
imperative.
Disclosure of Invention
The
invention aims to overcome the defects of the catalyst used for
preparing anhydrous formaldehyde at present, such as: the acidity and
the alkalinity of the catalyst are difficult to control, and a plurality
of byproducts are generated. The patent combines a palladium-indium
alloy with higher activity and a nano-silica carrier without a
significant acid center to prepare a silica-supported palladium-indium
catalyst. The catalyst has the advantages of simple preparation method,
high stability, mild reaction conditions and high conversion rate and
selectivity.
The
invention relates to a preparation scheme of anhydrous formaldehyde,
wherein the preparation of the anhydrous formaldehyde adopts PdIn/SiO2As
a catalyst, the catalyst was molded and charged into a reaction tube,
and then charged into a fixed bed reactor. Under normal pressure,
methanol is injected by an advection pump, inert gas is used as carrier
gas, the methanol feeding ratio is 10-60 vol%, and the methanol feeding
speed is 0.10-0.30 mL/(g)catMin), reacting at 350-600 ℃, and detecting a product on line by gas chromatography.
The PdIn/SiO2A catalyst, wherein the content of palladium is 0.5-5 wt% (by mass), and the content of indium is 0.5-5 wt%. The PdIn/SiO2The catalyst is prepared by a coprecipitation method and an impregnation method.
The PdIn/SiO2In
the preparation of the catalyst, the soluble precursor salt of
palladium is one or two of palladium nitrate, palladium ammonium nitrate
and sodium chloropalladate, and the soluble precursor salt of indium is
one or two of indium nitrate and indium chloride. The PdIn/SiO2In
the preparation of the catalyst, the soluble precursor salt of
palladium is preferably one or two of palladium ammonium nitrate and
sodium chloropalladate, and the soluble precursor salt of indium is
preferably indium chloride. The filling PdIn/SiO2The
thickness of the catalyst bed layer is 5-40 mm, the methanol feeding
ratio is 10-60 vol% (volume), and the methanol feeding speed is
0.10-0.30 ml/(g)catMin), the reaction temperature is 350-500 ℃. The inert gas is one or more of nitrogen, argon and helium.
This
patent discloses silica supported palladium indium catalysts with
higher catalytic activity. The active component palladium can activate
C-H bonds of methanol and O-H bonds of the methanol, and the
introduction of indium effectively adjusts the electronic structure and
spatial distribution of the palladium, inhibits the excessive
dehydrogenation of the target product formaldehyde at palladium sites,
and obviously improves the selectivity of the formaldehyde. And the
palladium-indium has no obvious acid site, so that the side reaction of
dimethyl ether and water generated by methanol dehydration catalyzed by
acid is avoided while methanol dehydrogenation is catalyzed, and the
high-purity anhydrous formaldehyde is favorably obtained. In addition,
the catalyst related to the patent adopts nano silicon oxide as a
carrier, has large surface area, is beneficial to high dispersion of
palladium and indium, is not easy to agglomerate and deactivate, and has
no obvious acid center, thereby avoiding side reaction caused by the
acid center and further improving the selectivity and stability of
preparing anhydrous formaldehyde by methanol dehydrogenation.
The specific implementation mode is as follows:
in
order to further explain the present invention in detail, several
specific embodiments are given below, but the present invention is not
limited to these embodiments.
Example 1
Coprecipitation method for preparing (0.5 wt% Pd-0.5 wt% In)/SiO2Catalyst, operating as follows: weighing 2g of nano SiO2(50nm), dispersing in 20mL of water, adding one eachQuantitative Na2PdCl4And InCl3·4H2O,
stirring for 1h, and adjusting the pH value of the suspension to 11 by
using 30% ammonia water. Stirring for 1H, centrifuging, washing to
neutrality, oven drying at 80 deg.C, and drying at 500 deg.C H2Reducing for 2h to obtain (0.5 wt% Pd-0.5 wt% In)/SiO2A
catalyst. 2g of the catalyst was weighed, tabletted, molded and packed
into a fixed bed reactor. Under normal pressure, nitrogen gas is used as
carrier gas, methanol is injected by an advection pump, the volume
ratio of the methanol is 10 vol%, the feeding speed of the methanol is
0.30mL/(gcat. min), the reaction is carried out at 350 ℃, the conversion
rate of the methanol is 73% by gas chromatography online detection, and
the selectivity of the formaldehyde is 66%.
Example 2
Coprecipitation method for preparing (0.5 wt% Pd-1.0 wt% In)/SiO2Catalyst, operating as follows: weighing 2g of nano SiO2(50nm), dispersing in 20mL of water, adding a certain amount of Na2PdCl4And InCl3·4H2O,
stirring for 1h, and adjusting the pH value of the suspension to 11 by
using 30% ammonia water. Stirring for 1H, centrifuging, washing to
neutrality, oven drying at 80 deg.C, and drying at 450 deg.C in H2Reducing for 2h to obtain (0.5 wt% Pd-1.0 wt% In)/SiO2A
catalyst. 2g of the catalyst was weighed, tabletted, molded and packed
into a fixed bed reactor. Under normal pressure, nitrogen gas is used as
carrier gas, methanol is injected by an advection pump, the volume
ratio of the methanol is 15 vol%, the feeding speed of the methanol is
0.25mL/(gcat. min), the reaction is carried out at 450 ℃, the conversion
rate of the methanol is 77% by gas chromatography online detection, and
the selectivity of the formaldehyde is 85%.
Example 3
Publication number
Priority date
Publication date
Assignee
Title
EP0130068A2
*
1983-06-23
1985-01-02
Sumitomo Chemical Company, Limited
A process for producing formaldehyde
US5103066A
*
1990-12-10
1992-04-07
Mobil Oil Corp.
Dehydrogenation of alcohols over non-acidic metal-zeolite catalysts
WO2008006792A1
*
2006-07-11
2008-01-17
Basf Se
A method for dehydrating alcohols
CN105170145A
*
2014-06-20
2015-12-23
中国科学院大连化学物理研究所
Catalyst for anoxic dehydrogenation of methanol, and application thereof
* Cited by examiner, † Cited by third party
Publication
Publication Date
Title
CN102227401B
2014-06-18
Carbonylation process for production of methyl acetate
CN106140156A
2016-11-23
A kind of activated carbon supported rhodium base catalyst and its preparation method and application
CN103508863B
2016-04-27
A kind of method preparing anhydrous formaldehyde
CN109999896B
2020-09-25
High-efficiency
catalyst applied to preparation of cyclohexanone by selective
hydrogenation of phenol and preparation method thereof
CN105732349A
2016-07-06
Method for preparing anhydrous formaldehyde through methanol dehydrogenation
CN105732350A
2016-07-06
Method of producing anhydrous formaldehyde through oxygen-free dehydrogenation
CN104447248A
2015-03-25
Preparation method for anhydrous formaldehyde
CN102580754A
2012-07-18
Catalyst for synthesizing methyl acetate as well as preparation method and application
CN111763145B
2021-11-16
Method for synthesizing acrylic acid from methyl acetate aqueous solution
CN107486191B
2020-06-23
Iridium-based catalyst loaded on acid-treated carbon carrier and preparation method and application thereof
CN101619048A
2010-01-06
Method for synthesizing propylene oxide
CN111217683A
2020-06-02
Method for preparing anhydrous formaldehyde by methanol dehydrogenation
CN102757310B
2015-04-29
Method of preparing isopropanol by catalytic conversion of cellulose
CN111763143A
2020-10-13
Method for synthesizing acrylic acid
CN111215062A
2020-06-02
Method for preparing anhydrous formaldehyde
CN109704917B
2023-09-15
Process for chemically converting corncob furfural residues into bioethanol
CN111217687A
2020-06-02
Method for preparing anhydrous formaldehyde
CN1024464C
1994-05-11
Method for preparing isoborneol by catalyzing camphene hydration with resin
CN110981698B
2022-04-19
Preparation method of 3-methyl-2-butenol
CN101502805B
2011-01-12
Catalyst for preparing acetic anhydride as well as preparation method and application
CN102249989B
2015-01-28
Method for preparing 3-methylpyridine by utilizing acrolein
CN102500420A
2012-06-20
Alcohol gas phase dehydrogenation catalyst, preparation method thereof and application
CN103480376B
2015-01-14
Preparation method and application of synthetic carboxylate copper-mesoporous zirconium bifunctional catalyst
*********************************************************************************************************************
CN111215062A
*
2018-11-27
2020-06-02
中国科学院大连化学物理研究所
Method for preparing anhydrous formaldehydeAbstract
The
invention relates to a method for preparing anhydrous formaldehyde. The
method employs a platinum indium catalyst (PtIn/SiO) supported on
silica2) The specific process is as follows: PtIn/SiO2Filling the
formed catalyst into a reaction tube, then filling the reaction tube
into a fixed bed reactor, injecting methanol by an advection pump under
normal pressure, taking inert gas as carrier gas, wherein the methanol
feeding ratio is 10-60 vol%, and the methanol feeding speed is
0.10-0.30 mL/(g)cat.Min), reacting at 400-650 ℃, and obtaining the
conversion rate of the methanol of 65-90% and the selectivity of the
formaldehyde of 60-85% by chromatography. The invention relates to a
method for preparing anhydrous formaldehyde by adopting PtIn/SiO2As the
catalyst, the catalyst has higher catalytic activity and product
selectivity, less by-products, simple preparation process and high
thermal stability.
Example 2Coprecipitation
method for preparing (0.5 wt% Pt-1.0 wt% In)/SiO2Catalyst, operating as
follows: weighing 2g of nano SiO2(50nm), dispersing in 20mL of water,
adding a certain amount of Na2PtCl4And InCl3·4H2O, stirring for 1h, and
adjusting the pH value of the suspension to 11 by using 30% ammonia
water. Stirring for 1H, centrifuging, washing to neutrality, oven
drying at 80 deg.C, and drying at 450 deg.C in H2Reducing for 2h to
obtain (0.5 wt% Pt-1.0 wt% In)/SiO2A catalyst. 2g of the catalyst was
weighed, tabletted, molded and packed into a fixed bed reactor. Under
normal pressure, nitrogen gas is used as carrier gas, methanol is
injected by an advection pump, the volume ratio of the methanol is 15
vol%, the feeding speed of the methanol is 0.25mL/(gcat. min), the
reaction is carried out at 450 ℃, the conversion rate of the methanol
is 77% by gas chromatography online detection, and the selectivity of
the formaldehyde is 85%.*****************************************************************************************************
CN111217683A
2020-06-02
Method for preparing anhydrous formaldehyde by methanol dehydrogenation
Abstract
The
invention relates to a method for preparing anhydrous formaldehyde by
methanol dehydrogenation. The method adopts a palladium-indium catalyst
(PdIn/SiO) supported by silicon dioxide2) The specific process is as
follows: PdIn/SiO2Filling the formed catalyst into a reaction tube,
then filling the reaction tube into a fixed bed reactor, injecting
methanol by an advection pump under normal pressure, taking inert gas
as carrier gas, wherein the methanol feeding ratio is 10-60 vol%, and
the methanol feeding speed is 0.10-0.30 mL/(g)cat.Min), reacting at
350-600 ℃, and obtaining the conversion rate of the methanol of 60-80%
and the selectivity of the formaldehyde of 65-85% by chromatography.
The invention relates to a method for preparing anhydrous formaldehyde
by methanol dehydrogenation, which adopts PdIn/SiO2As the catalyst, the
catalyst has higher catalytic activity and product selectivity, less
by-products, simple preparation process and high thermal stability.
Background
Formaldehyde
is an important organic chemical raw material, can be used for
producing thermosetting resins such as phenolic resin and melamine
resin, and bulk chemicals such as polyformaldehyde, phenolic aldehyde,
urotropine and 1, 4-butanediol, and is also a raw material for
synthesizing products such as dye, pesticide, disinfectant and adhesive.
At present, the methanol oxidation method is generally adopted industrially to
prepare formaldehyde, theoretically, a formaldehyde aqueous solution
with the molar ratio of 1:1 is obtained, the vapor pressure of the
formaldehyde aqueous solution is low, the formaldehyde and water form
an azeotrope, the separation and purification of the formaldehyde are
very difficult, and the energy consumption is huge. In recent years,
the demand of engineering plastics, urotropine and other medicines with
excellent synthesis performance on anhydrous formaldehyde is
increasing, and the anhydrous formaldehyde is obtained by removing
moisture from industrial formaldehyde aqueous solution at present, so
that the direct preparation of the anhydrous formaldehyde is a hot
point of research.
The
process for preparing formaldehyde by anaerobic dehydrogenation of
methanol obtains formaldehyde and byproduct hydrogen, the formaldehyde
and the byproduct hydrogen are easy to separate, and the hydrogen is
industrial gas with high added value; the process has no water
generation, avoids the separation operation of the formaldehyde aqueous
solution, and greatly saves the purchase cost and the operation cost of
the rectification equipment; the process also avoids the problem that
the formic acid generated by the methanol oxidation method corrodes
equipment. Therefore, the direct dehydrogenation of methanol to prepare
formaldehyde is a process with great industrial prospect.
In
recent years, a new anhydrous formaldehyde preparation process with
remarkable economic benefit draws high attention at home and abroad,
and a great deal of research work is brought forward. Research efforts
are currently focused on the development of highly efficient catalysts,
including metals and their oxides, alkali metal salts, and molecular
sieves, among others. CN102274722A discloses a new type V2O3And a load
type V2O3The preparation method shows better activity in the
dehydrogenation reaction of methanol. Takagi et al (Takagi K, Morikawa
Y, Ikawa T.Chemestryletters, 1985, 14: 527-0Has high selectivity to
formaldehyde. CN101961650A discloses a homogeneous coprecipitation
method for preparing zirconium-based catalyst and catalyzing methanol
to perform anaerobic dehydrogenation, wherein the yield of formaldehyde
reaches 60%. Davirin et al (CN1390639A, CN1537673A, CN1544147A)
disclose a series of preparation methods of silver-based catalysts for
direct dehydrogenation of methanol. The patent CN101147872A takes
industrial sodium bicarbonate as a raw material to prepare the
anhydrous formaldehyde by catalyzing and preparing the industrial
sodium carbonate, and lays a foundation for the industrialization of
preparing the formaldehyde by methanol dehydrogenation. Music et al
(Music A, Batista J, Levec J. appliedCatalysis A: general, 1997, 165:
115-131) takes a ZSM-5 molecular sieve catalyst as a matrix, and
prepares Na-ZSM-5 and Cu-ZSM-5 type molecular sieves by an ion exchange
method, thereby obtaining better selectivity in the methanol
dehydrogenation reaction. CN105601487A discloses a rare earth complex
Ln [ CH ]2(CH2)nR]3·xH2O.yL, the catalyst has higher selectivity to
formaldehyde.
Based
on the above, the disadvantages of the catalysts currently used for the
preparation of anhydrous formaldehyde are: copper particles in the
copper-based catalyst are distributed unevenly, are larger, have
smaller active surface area and lower activity; the modified molecular
sieve catalyst is difficult to regulate and control in acid-base
property and has more byproducts; the catalytic activity of
conventional carbonates or bicarbonates is relatively inert and the
reaction temperature is generally above 700 ℃. The complex catalyst is
a homogeneous catalysis process, and the separation energy consumption
is large. Therefore, a heterogeneous catalytic system with good
stability, high activity and formaldehyde selectivity and mild reaction
conditions is developed, and the preparation of anhydrous formaldehyde
by methanol dehydrogenation is imperative.
Disclosure of Invention
Example 3Coprecipitation
method for preparing (1.5 wt% Pd-0.5 wt% In)/SiO2Catalyst, operating as
follows: weighing 2g of nano SiO2(50nm), dispersing in 20mL of water,
adding a certain amount of Na2PdCl4And InCl3·4H2O, stirring for 1h, and
adjusting the pH value of the suspension to 11 by using 30% ammonia
water. Stirring for 1H, centrifuging, washing to neutrality, oven
drying at 80 deg.C, and drying at 500 deg.C H2Reducing for 2h to obtain
(1.5 wt% Pd-0.5 wt% In)/SiO2A catalyst. 2g of the catalyst was weighed,
tabletted, molded and packed into a fixed bed reactor. Under normal
pressure, nitrogen gas is used as carrier gas, methanol is injected by
an advection pump, the volume ratio of the methanol is 30 vol%, AThe
alcohol feeding speed is 0.20mL/(gcat. min), the reaction is carried
out at 450 ℃, the conversion rate of the methanol is 60 percent by gas
chromatography on line detection, and the selectivity of the
formaldehyde is 75 percent.***************************************************************************************************
(CN1390639A, CN1537673A, CN1544147A)CN1390639A 2002 Current Assignee Fudan University
Abstract
A
carried silver catalyst for preparing anhydrous formaldehyde by
directly dehydrogenating methanol is prepared by sol-gel method, which
includes such steps as mixing ethyl n-silicate with the solution
containing soluble Mg salt, dropping it in aqueous solution of
inorganosilver salt, generating colloid, aging, drying and calcining.
Its advantages are high activity, long service life and low cost.
Background technology
Formaldehyde
is the important foundation raw material of chemical industry, is
widely used in the intermediate product of chemical products such as
producing acetal resin, Lauxite, phenolic resins, pentaerythrite,
methenamine and medicine and agricultural chemicals.And in these
fields, most of formaldehyde products of using is anhydrous
formaldehyde.As producing anhydrous formaldehyde, then need moisture
commodity formaldehyde is carried out distillation operation.This not
only needs to drop into comparatively considerable equipment, operating
cost, but also, cause forming azeotropic system, thereby in actual
distillation operation process because formalin relative ideal solution
is the minus deviation of certain value, the dehydration separating
effect is not good enough, and production cost is high.Utilizing the
methyl alcohol direct dehydrogenation to synthesize anhydrous
formaldehyde, then is a kind of new process of remarkable in economical
benefits.At first, this method does not have water to generate, and can
save rectifying device investment and operating cost thereof; But next
by-product high-quality hydrogen, and hydrogen is easy to separate from
reaction system.It is this that to produce in the anhydrous
formaldehyde method crucial technology by the methyl alcohol direct
dehydrogenation partly be the catalyst that is adopted, existing patent
report is by the molten zinc of zinc, potassium, indium or the
aluminium of the catalyst of being made up of copper, silver, silicon
(special public clear 41-11853), fusion or the alloy of these metals
(special public clear 47-19251), carbon containing or contain the alloy
(spy opens clear 48-97808) of zinc and the catalyst (spy opens clear
52-215) be made up of copper, zinc, selenium etc., but these methods
have various shortcoming such as catalyst life is short, reactivity is
low, do not have industrial application value.In addition, the catalyst
that use is made up of copper, zinc, sulphur (spy opens clear 51-1407)
and form catalyst by copper, zinc, supply gas state sulfide carries out
the method (spy opens clear 51-76209) of methanol dehydrogenation,
sneak into sulphur in reaction product or discharge gas, this do not
have industrial prospect to the disagreeableness catalyst of
environment.A kind of use of catalyst containing sodium makes the
formaldehyde yield bring up to 70% (Appl.Catal.2001 (213) 203), but
owing to problems such as reaction temperature and catalyst life and
regeneration have limited its industrial applications.
Can test with the following method activity of such catalysts provided by the invention:
The
present invention adopts the fixed bed flow method to investigate
catalyst activity.By Bubbling method methanol steam (vapourizing
temperature is 30~60 ℃) is sent into reactor and contact 450~750 ℃ of
reaction temperatures, H in reacted methanol content, content of
formaldehyde and the tail gas with catalyst 2, CO and CO 2Content
measure by gas chromatography respectively.
Reactor
is that an internal diameter is 4.5 millimeters a quartz ampoule, and
the novel load silver catalyst that makes places the reaction tube
constant temperature zone, and catalytic bed temperature is measured
with nickel chromium-nickel silicon thermocouple, and the point for
measuring temperature of thermocouple places catalytic bed bottom
centre place.
The
temperature of the outer electric furnace of conditioned reaction
device makes the reaction temperature of catalytic bed be stabilized in
required numerical value.Among the present invention, reaction
condition should be controlled at appropriate value.The reaction bed
temperature is between 450~750 ℃.The catalyst bed layer height is
between 5~50mm.The reacting gas air speed is controlled at 1 * 10 4~30
* 10 4Hr -1Between (under the standard state).
Embodiment
1: take by weighing the 0.75g silver nitrate and be dissolved in 100mL
water, add 5.56g Mg (NO 3) 26H 2O, treat that dissolving is placed in
the 250mL three-necked bottle, dropwise add the 33mL ethyl
orthosilicate, simultaneously violent electromagnetic agitation is kept
70 ℃ of oil bath temperatures, and adding 50mL gelatinizing
agent~isopropyl alcohol, load onto reflux condensing tube, stir
colloidal sol curing after three hours, stop to stir, be warming up to
100 ℃, evaporating solvent 12 hours.Be transferred to a crucible,, be
transferred to 700 ℃ of roastings of muffle furnace 6 hours then, be
crushed to 40~60 orders, can get the Ag-SiO of silver content 5% with
infrared lamp baking 24 hours 2-MgO catalyst is designated as the 1#
catalyst.
Embodiment
2: take by weighing the 1.5g silver nitrate and be dissolved in 100mL
water, add 5.56g Mg (NO 3) 26H 2O, treat that dissolving is placed in
the 250mL three-necked bottle, disposable adding 33mL ethyl
orthosilicate, simultaneously violent electromagnetic agitation is kept
75 ℃ of oil bath temperatures, and adding 50mL gelatinizing
agent~ethanol, load onto reflux condensing tube, stir colloidal sol
curing after six hours, stop to stir, be warming up to 90 ℃,
evaporating solvent 24 hours.Be transferred to a crucible,, be
transferred to 650 ℃ of roastings of muffle furnace 10 hours then, be
crushed to 40~60 orders, can get the Ag-SiO of silver content 10% with
infrared lamp baking 24 hours 2-MgO catalyst is designated as the 2#
catalyst.